A daily 5-minute safety discussion provides over 20 hours of vital safety education yearly for each employee. This simple practice explains why toolbox talk topics have become indispensable to workplace safety programs in a variety of industries.
Safety moments, tailgate meetings, or toolbox talks – whatever you call them – these brief yet impactful sessions make the most important difference. Companies that hold regular safety talks report fewer workplace injuries than those that skip them.
Our team has compiled 47 must-cover safety meeting topics to help protect your workers, ranging from the “Fatal Four” hazards in construction to proper PPE usage. These carefully selected topics address common workplace risks and build a stronger safety culture in your organization.
Personal Protective Equipment (PPE) Essentials

Image Source: tradesafe
Personal protective equipment serves as the final defense against workplace hazards. The right selection and upkeep is vital for worker safety. A new OSHA rule will take effect from January 15, 2025, stating that all PPE must fit correctly to give intended protection.
PPE Selection Guidelines
The right PPE starts with getting a full picture of workplace hazards. Safety standards should take priority over comfort, though both play vital roles to ensure workers keep using their gear. The core team must verify that PPE meets or goes beyond ANSI standards.
Common PPE Mistakes
The biggest problem comes from thinking PPE is one-size-fits-all. Standard sizes don’t work for everyone’s body type, which puts workers at risk of exposure to workplace hazards. Lab coats worn outside designated areas and reused disposable gloves can also create contamination risks.
PPE Maintenance Best Practices
Good maintenance will boost PPE lifespan and keep protection levels high. Your maintenance schedule should include:
- Checks before each use
- Cleaning as specified by manufacturers
- Storage in clean, dry spots away from sunlight
- Records of all maintenance work
When to Replace PPE
You need to know the right time to replace protective gear to keep safety levels high. Look for these signs:
- Hard hats need a new shell every 2-5 years and suspension yearly
- Safety footwear shows cracks, holes, or separating materials
- Gloves have wear marks, stains, or don’t fit like before
- Foam earplugs need daily changes in dusty areas
- Fall protection gear needs replacement right after any fall
A grading system can help assess PPE condition and boost workplace safety. Remove and replace any equipment with low grades immediately. On top of that, replace any PPE involved in incidents right away, whatever the visible damage, to maintain the best protection.
Fall Protection Fundamentals

Image Source: BigRentz
Falls are one of the main causes of traumatic deaths at work. They make up eight percent of all workplace fatalities from trauma. Every workplace safety program must include basic fall protection knowledge.
Types of Fall Protection Systems
Fall protection systems come in two categories: passive and active systems. Passive systems like guardrails and safety nets protect workers automatically. Active systems require workers to participate and include personal fall arrest systems, positioning devices, and fall restraint equipment.
Fall Protection Equipment Inspection
Equipment inspections play a vital role in fall protection. OSHA requires two types of inspections:
- Pre-use inspection during each workshift
- Annual inspection by a Competent Person
Annual inspection documents must include:
- Equipment description and model number
- Manufacturer details
- Serial number
- Date of manufacture
- Inspection date
- Inspector’s name and signature
Common Fall Hazards
Research shows that falls from heights of 10 feet or more almost always cause serious injury or death. In spite of that, falls under ten feet can also result in serious injuries. OSHA sets different fall protection thresholds by industry:
- General Industry: 4 feet
- Maritime: 5 feet
- Construction: 6 feet
An OSHA study of 99 fall-related fatalities showed that proper use of these safety measures could have prevented almost all deaths:
- Guardrails
- Body harnesses
- Safety nets
- Protective covers
Employers must ensure fall protection equipment meets specific force requirements to improve safety:
- Personal fall arrest system components need a minimum tensile load of 5,000 pounds per user
- Self-retracting lanyards require 3,000 pounds tensile strength
- Construction anchorages and lanyards just need 5,400 pounds breaking strength
Electrical Safety Protocols

Image Source: MySafetySign.com
Electrical incidents lead to about 1,000 deaths and 30,000 non-fatal shocks each year in the United States. Every workplace safety program must include proper electrical safety protocols.
Simple Electrical Safety Rules
A clean and orderly work area creates the foundation of electrical safety. You need to follow these safety practices:
- Use insulated hand tools and double-insulated power tools
- Take off metal jewelry and watches before electrical work
- Install Ground Fault Interrupters (GFIs) near wet areas
- Check tools for damaged power cords before use
Lockout/Tagout Procedures
Workers stay safe from unexpected energy release through proper lockout/tagout (LOTO) practices. Authorized employees must complete these steps before maintenance work:
- De-energize the machine
- Lock out disconnect switches
- Tag the disconnect switches
- Test the machine to confirm it’s off
- Keep the key until work is done
Authorized employees get standardized locks with their own keys that they use only for LOTO procedures. Each tag must show the employee’s name and date clearly.
Emergency Response for Electrical Incidents
Quick action saves lives after an electrical shock. Minor shocks require you to take the person to Health Services after telling supervisors. You must call emergency services right away if the victim shows:
- Loss of consciousness
- Can’t let go due to prolonged contact
- Falls or trauma
- Clear burn injury
- High voltage exposure (>750 volts)
First responders should not touch shock victims until the power is off. They should use non-conductive items like wooden planks or plastic broomhandles to separate victims from electrical sources. Once the scene is safe, check breathing and pulse, then start CPR if needed.
Good documentation of electrical incidents helps teams understand why accidents happen and prevent future ones. Teams can reduce electrical hazards at work by following safety protocols and responding quickly to emergencies.
Fire Safety and Prevention

Image Source: First-Line Fire Extinguisher
Fire incidents at offices and stores led to USD 932 million in direct property damage from 16,500 cases in 2020. Proper fire safety protocols play a vital role to protect lives and keep businesses running.
Fire Extinguisher Types and Usage
Fire extinguishers fall into five main categories based on the fires they fight:
- Class A: For ordinary materials like wood, paper, and cloth
- Class B: For flammable liquids and gasses
- Class C: For electrical equipment
- Class D: For flammable metals
- Class K: For cooking oils and fats
Most workplaces can rely on multipurpose extinguishers with “A-B-C” labels. The “UL Listed” label on these devices proves certification from nationally recognized testing labs.
Emergency Evacuation Procedures
A good evacuation plan needs clear roles and responsibilities. These are the must-have elements:
- Clear Chain of Command: Fire wardens help others and keep track of personnel
- Primary and Secondary Routes: Routes should stay well-lit, clear, and marked properly
- Assembly Points: Meeting spots must be at least 100 feet away from the building
- Head Count Protocol: Someone needs to count all employees, visitors, and contractors after evacuation
Fire Prevention Tips
Smart prevention steps cut down fire risks significantly. Here’s what works best:
- Fire protection systems should follow NFPA standards
- Regular checks for dust hazards where combustible materials are present
- Special fire systems work best for oil-cooled transformers and hydraulic equipment
- Good airflow matters when using flammable liquids
Workplace safety improves with designated smoking areas away from buildings and commercial smoking receptacles. Flammable liquids need storage in UL-listed safety containers with proper ventilation.
Fire protection equipment needs regular checks to work right. This means testing sprinklers, keeping paths to fire extinguishers clear, and making sure alarms work properly. Companies that stick to these rules protect their workers and assets better while keeping fire risks low.
Hazardous Material Handling

Image Source: Princeton EHS – Princeton University
Managing hazardous materials is the life-blood of workplace safety, especially when these substances can pose serious risks to human health and the environment.
Chemical Safety Guidelines
The first significant step in chemical safety involves identifying hazardous materials. Warning labels with words like CAUTION, WARNING, DANGER, or POISON help in identification. The simple guidelines include:
- Maintaining accurate chemical inventories
- Ensuring proper labeling of all containers
- Keeping Material Safety Data Sheets available
- Training staff regularly on handling procedures
Proper Storage Techniques
Safe storage requires careful attention to detail. Hazardous materials should be stored in designated areas that meet these criteria:
- Away from high-traffic zones and unauthorized access
- Protected from rain, flooding, or vandalism
- Equipped with proper ventilation systems
- Furnished with appropriate storage foundations
- Supplied with adequate aisle space for inspections
Spill Response Procedures
Quick action after chemical spills is vital. A complete spill response plan should outline:
- Original Assessment Steps:
- Alert area occupants and supervisors
- Review spill size and hazard level
- Determine need for evacuation
- Containment Protocol:
- Don appropriate PPE before approaching
- Protect floor drains from contamination
- Use designated spill control materials
PPE for Chemical Handling
Chemical handling needs specific protective equipment based on hazard assessment. Four essential protection levels exist:
Level A: For highest exposure risk
- Full-face SCBA
- Totally encapsulated chemical suit
- Inner and outer chemical-resistant gloves
Level B: For high respiratory risks
- Hooded chemical-resistant clothing
- Face shield
- Chemical-resistant boots
Level C: For known airborne substances
- Full-face air purifying respirators
- Chemical-resistant gloves
- Emergency escape mask
Level D: For minimal contamination risk
- Basic coveralls
- Safety glasses
- Chemical-resistant footwear
Regular PPE inspection and maintenance will give optimal protection against chemical exposure. Organizations can minimize risks associated with hazardous material handling by implementing these protocols properly.
Machine Guarding Safety

Image Source: RPF Environmental
Each year, machine operators suffer around 18,000 injuries including amputations, lacerations, crushing injuries, and abrasions. The situation becomes even more serious with 800 deaths occurring due to poor machine guarding. Machine safeguarding plays a crucial role to prevent these devastating workplace incidents.
Types of Machine Guards
We can classify machine guards into five distinct categories that provide detailed protection:
- Fixed Guards: These barriers attach permanently and need tools to remove them. They work best for power transmission devices and areas that rarely need maintenance access
- Interlocked Guards: The machinery shuts down automatically when these guards open. They suit equipment that needs frequent access
- Adjustable Guards: These barriers modify to fit different material sizes. Drill presses and band saws commonly use them
- Self-Adjusting Guards: These barriers adapt automatically to different material sizes and improve both safety and productivity
- Presence-Sensing Guards: These employ sensors to detect and stop human entry into dangerous zones
Maintenance Requirements
A systematic approach helps maintain these guards effectively. Key practices include:
- Regular checks of mounting points and guard integrity
- Records of all installations, modifications, and repairs
- Quick replacement of damaged or missing parts
- Use of manufacturer-recommended lubricants
- Guard alignment checks after maintenance
Common Violations
Manufacturing industries account for 80% of machine guarding violations according to OSHA data. The most common citations include:
- Poor point of operation guarding (1,089 violations)
- Loose or improperly secured guards (402 violations)
- Fixed machinery without proper anchoring (57 violations)
- Rotating drums and containers lacking protection (13 violations)
Guards must stop contact with dangerous parts and stay firmly attached. They should protect against falling objects without creating new hazards. Companies can reduce machine-related injuries and meet safety standards by implementing these safeguards properly.
Ladder Safety Basics

Image Source: tradesafe
Ladder accidents take over 300 lives and cause 164,000 injuries every year in the United States. The statistics show that ladders play a role in 43% of fatal falls. Safety fundamentals are vital to prevent workplace incidents.
Ladder Selection Guide
The right ladder choice depends on several factors. You need to think about the duty rating that fits your needs:
- Type IAA (Special Duty): 375 pounds
- Type IA (Extra Heavy Duty): 300 pounds
- Type I (Heavy Duty): 250 pounds
- Type II (Medium Duty): 225 pounds
- Type III (Light Duty): 200 pounds
Your work environment determines the best material choice. Aluminum ladders are lightweight and durable but can be dangerous near electricity. Fiberglass or wooden ladders are a safer bet around electrical sources.
Setup and Usage
The right positioning starts with the 1:4 ratio rule. The ladder’s base should be one foot away from the wall for every four feet of working length. Here are the key safety guidelines:
- Keep three-point contact (two hands and one foot, or two feet and one hand)
- Face the ladder while climbing
- Stay centered between side rails
- Don’t carry tools while climbing
- Make sure the ladder extends three feet above landing surfaces
Inspection Points
Regular checks are a vital part of ladder safety. Look out for:
- Structural Issues:
- Missing or loose steps/rungs
- Damaged side rails
- Worn non-slip feet
- Loose hardware components
- Surface Conditions:
- Oil, grease, or slippery materials
- Paint that might hide defects
- Signs of corrosion or rust
If you find defects, tag the ladder with “Do Not Use” or similar warning right away. Take it out of service and let authorized personnel handle repairs. These safety protocols help organizations reduce ladder-related incidents and keep the workplace safe.
Confined Space Entry

Image Source: Chemical Tweak
Working in confined spaces creates unique challenges because these areas often have hazardous atmospheres that can quickly threaten lives. A confined space needs a permit if it has what it all means like engulfment materials, hazardous atmospheres, or inwardly converging walls.
Permit Requirements
Every confined space entry just needs a detailed permit that documents everything in safety measures. The permit must list:
- Hazards present in the space
- Measures used to control and isolate hazards
- Acceptable entry conditions
- Testing equipment requirements
- Communication protocols
Air Testing Protocols
Atmospheric testing serves two clear purposes: the original evaluation and ongoing verification. Testing must follow this specific sequence:
- Oxygen levels (test first since most gas meters rely on proper oxygen levels)
- Combustible gasses and vapors
- Toxic gasses and vapors
Testing should happen at 4-foot intervals in the direction of travel and to each sides for stratified atmospheres. The operation requires continuous monitoring and proper ventilation to keep atmospheric conditions safe.
Emergency Procedures
Quick response saves lives during confined space emergencies. Key emergency protocols include:
- Calling rescue services right away
- Stopping unauthorized rescue attempts
- Following documented rescue steps
- Keeping communication open between entrants and attendants
A rescue plan should spell out specific roles, equipment locations, and communication protocols. Attendants must stay outside the confined space during emergencies and call trained rescue teams instead.
Required Equipment
OSHA requires specific equipment for confined space operations:
- Full-body harness with retrieval line
- Mechanical retrieval devices for vertical spaces deeper than 5 feet
- Appropriate respiratory protection
- Gas monitoring equipment
- Communication devices
- Ventilation systems
Regular inspection and maintenance keeps all rescue equipment working properly. Personal fall arrest system’s components must handle a minimum tensile load of 5,000 pounds per user.
Ergonomics at Work

Image Source: Pass The OT
Businesses lose over USD 20 billion in workers’ compensation and USD 100 billion in productivity each year due to musculoskeletal disorders. Proper ergonomic practices play a vital role in workplace safety and employee well-being.
Proper Lifting Techniques
Safe lifting requires a full picture of the situation. You should check the path for obstacles, know the weight of the load, and plan where to place it. Here’s how to lift safely:
- Keep loads between shoulders and upper thighs
- Hold items close to your body and tighten your abs
- Push instead of pull when possible
- Don’t lift items more than 15 times per minute
Workstation Setup
A well-laid-out workstation reduces strain on muscles, nerves, and joints. These adjustments will help:
- Chair Configuration:
- Set the height to keep feet flat on floor
- Adjust armrests until shoulders relax
- Keep backrest angle between 100-110 degrees
- Monitor Placement:
- Put screen right behind keyboard
- Place top third at eye level while seated
- Keep screen at arm’s length
Repetitive Motion Prevention
Similar movements over long periods often lead to strain injuries. Organizations can reduce these risks with proper prevention strategies. Here are the best practices:
- Take 1-2 minute stretch breaks every 20-30 minutes
- Change tasks for 5-10 minutes every hour
- Use ergonomic tools like headsets for long calls
- Install adjustable keyboard trays to get the right position
Companies should train employees about proper posture and positioning to improve protection. Regular workplace checks help spot potential risks before injuries happen. These ergonomic principles help organizations reduce workplace injuries and boost productivity when applied consistently.
Hand and Power Tool Safety

Image Source: SlideServe
Hand and power tool accidents injure more than one million people each year. These injuries result in USD 15.40 million in medical expenses and lost work time. Teams can reduce these incidents by following proper selection, maintenance, and operation guidelines.
Tool Selection
The right tool must match its specific task. Power tasks work best with single-handle tools that have handle diameters between 1¼ to 2 inches. Tools for precision work should have handle diameters of ¼ to ½ inch. Double-handled tools used in power tasks need grip spans of at least 2 inches when closed and no more than 3½ inches when open.
Maintenance Requirements
Tool safety and longevity depend on proper maintenance. These key practices cover:
- Clean tools after each shift with compressed air for vents
- Use manufacturer-specified lubricants on moving parts
- Keep equipment in dry, clean spaces
- Check carbon brushes, drive belts, and power cords for wear
- Control lithium-ion battery’s heat exposure
Daily maintenance routines and scheduled recalibration based on manufacturer specs help achieve the best performance. Battery-powered tools need climate-controlled storage areas and protection from moisture that could harm electrical components.
Safe Operation Guidelines
Safety depends on following proven protocols consistently. These essential practices include:
- Pre-operation checks:
- Look for tool damage before use
- Check proper grounding or double insulation
- Make sure guards are secure
- Operation safeguards:
- Keep work areas well-lit
- Install ground fault circuit interrupters in damp areas
- Protect cords from heat, oil, and sharp edges
- Unplug tools while changing accessories
Employers should train new staff on proper tool selection, maintenance procedures, and safe operation. Organizations can reduce tool-related injuries and maintain workplace safety standards by implementing these guidelines systematically.
Vehicle and Equipment Safety
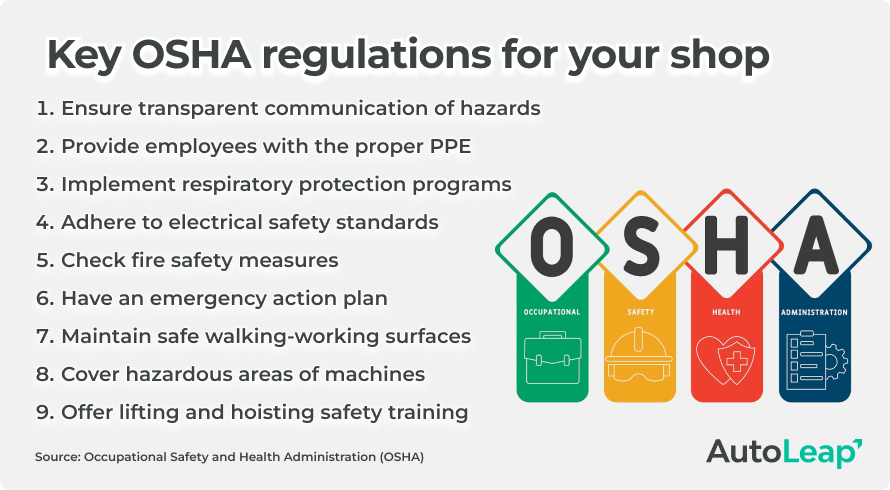
Image Source: AutoLeap
Safety protocols play a vital role in vehicle and equipment operation. Statistics reveal that poor maintenance and inspection lead to most workplace accidents. A systematic safety approach prevents downtime and protects operators.
Pre-operation Checks
Operators must complete a 360° walk-around inspection before they start work. The inspection should focus on:
- Fluid levels and possible leaks
- Tire condition and pressure
- Warning lights functionality
- Brake system performance
- Steering mechanism’s response
Safe Operating Procedures
The operator’s safety depends on maintaining three points of contact during equipment entry and exit. The core guidelines include:
- Setting controls to neutral and engaging parking brake before startup
- Checking all gages and warning devices work properly
- Using only designated operator stations
- Keeping clear communication with ground staff
- Staying away from parallel slopes or embankments
Maintenance Schedules
Equipment longevity relies on consistent maintenance. The schedule depends on:
- Time intervals (specific number of days)
- Mileage accumulation
- Engine hours for heavy-duty equipment
Company Policies
Clear vehicle safety protocols must exist in every organization. The policy should cover:
- Valid driver’s license requirements
- No mobile device usage during operation
- Mandatory seat belt use
- Regular driver evaluations
- Clear accident reporting steps
Testing Procedures
Equipment testing must meet manufacturer’s specs and regulatory requirements. The protocols verify:
- Brake system functionality
- Steering response
- Emergency shutdown systems
- Warning device operation
- Load capacity compliance
Support Programs
A complete support system boosts safety standards. The program should feature:
- Regular operator training
- Equipment-specific certifications
- Preventive maintenance tracking
- Performance monitoring systems
- Emergency response protocols
These safety measures help organizations reduce equipment-related incidents. Updated safety protocols ensure industry standard compliance and protect operators.
Scaffolding Safety

Image Source: Safety Evolution
Much of workplace injuries come from scaffolding accidents, but the right safety protocols can prevent most of these incidents. Each part of a scaffold must be strong enough to handle four times its maximum intended load.
Assembly Requirements
The first step in safe scaffold assembly is to look at the work site for overhead objects, falling hazards, uneven ground, and doorways. You need to follow these key assembly steps:
- Put base plates with mud sills on dirt surfaces
- Keep the height-to-base width ratio under 4:1
- Add guying, tying, or bracing to secure scaffolds that go beyond 4:1 ratio
- Make sure footings stay level, sound, and rigid
Inspection Checklist
A competent person should check the scaffold daily to keep it safe. The key inspection points cover:
Platform Safety:
- Planks should cover the whole platform with gaps under 1 inch
- Platforms must be at least 18 inches wide
- Planks should not stick out more than 12 inches past supports
- Work areas need to stay clear of debris, mud, or tripping hazards
Structural Integrity:
- Check if guardrail systems are properly installed
- Look at tie-ins and bracing
- Check all mounting points
- Look for wear on components
Fall Protection on Scaffolds
OSHA says workers need fall protection when they work on scaffolds higher than 10 feet above lower levels. Different scaffolds need different protection:
Single-point and two-point adjustable suspension scaffolds just need both guardrail systems and personal fall arrest systems. Supported scaffolds must have either:
- Guardrail systems that can take 200 pounds of force
- Personal fall arrest systems with harnesses, D-rings, and strong anchor points
Workers must learn from qualified people about scaffold hazards, control methods, and how to use everything safely. Companies that follow these safety rules carefully will have fewer scaffold accidents and stay within regulations.
Excavation and Trenching

Image Source: OSHA.com
Trench collapses take 19 lives each year, but these deaths could be prevented with proper protective systems. Workers need to know soil types and safety measures to work safely during excavation.
Soil Classification
OSHA divides soil into four types based on stability:
- Stable Rock: Natural solid mineral matter
- Type A: Cohesive soils with unconfined compressive strength of 1.5 tsf or greater
- Type B: Cohesive soils between 0.5 tsf and 1.5 tsf
- Type C: Cohesive soils with strength of 0.5 tsf or less
Competent personnel must perform visual and manual soil classification. They should examine excavated material and trench walls visually, while manual tests help assess soil strength through thumb penetration or ribbon tests.
Protection Systems
OSHA requires protective systems for trenches deeper than 5 feet unless the excavation is in stable rock. Workers can use four main protection methods:
- Sloping: Cutting trench walls at angles away from excavation
- Shoring: Installing aluminum hydraulic supports
- Shielding: Using trench boxes
- Benching: Creating horizontal levels in trench walls
Several significant factors determine the choice of protective systems:
- Soil classification results
- Excavation depth
- Water content
- Weather conditions
- Nearby operations
Access and Egress
Worker safety depends on reliable entry and exit routes. The core requirements cover:
- Access points within 25 feet of workers in trenches 4 feet or deeper
- Ladders that extend 3 feet above landing surfaces
- Structural ramps with non-slip surfaces
- Ramps with cleats where steps are needed
Competent personnel should inspect the site daily to eliminate excavation hazards. Organizations can minimize trench-related incidents and meet regulatory requirements by following proper soil classification, using protection systems, and maintaining access protocols.
Respiratory Protection

Image Source: CDC Blogs
Millions of workers rely on respirators to protect them from insufficient oxygen, harmful dusts, gasses, and sprays. The right respiratory protection is vital for their safety.
Respirator Selection
A full picture of exposure risks should guide your respirator choice. You need to identify the types of contaminants – whether they’re particulates, gasses, vapors, or biological hazards. Personal monitoring and objective data help determine exposure levels. Particulate hazards require filters from these three categories:
- N-series: Not resistant to oil
- R-series: Oil resistant up to 8 hours
- P-series: Oil-proof with 40-hour usage limit
Fit Testing Requirements
OSHA requires fit testing before the original respirator use and yearly after that. Workers can use two main testing methods:
Qualitative Testing: Workers detect leaks through their senses using:
- Isoamyl acetate (banana smell)
- Saccharin (sweet taste)
- Bitrex (bitter taste)
- Irritant smoke
Quantitative Testing measures actual leakage with specialized instruments. Both methods need seven specific exercises that last one minute each. The test results must be properly documented.
Maintenance and Storage
Good care makes respirators last longer and provides better protection. The maintenance process should include:
- Regular Inspection:
- Look for cracks or distortion in the face piece
- Check the head straps’ elasticity
- Make sure valves work properly
- Look at filter condition
- Storage Requirements:
- Keep in sealed containers
- Keep away from sunlight, heat, moisture
- Store separately from chemicals
- Prevent face piece deformation
Clean respirators after each use according to manufacturer guidelines to improve protection. Organizations can protect workers from respiratory hazards and meet regulations by following these protocols systematically.
Noise Protection
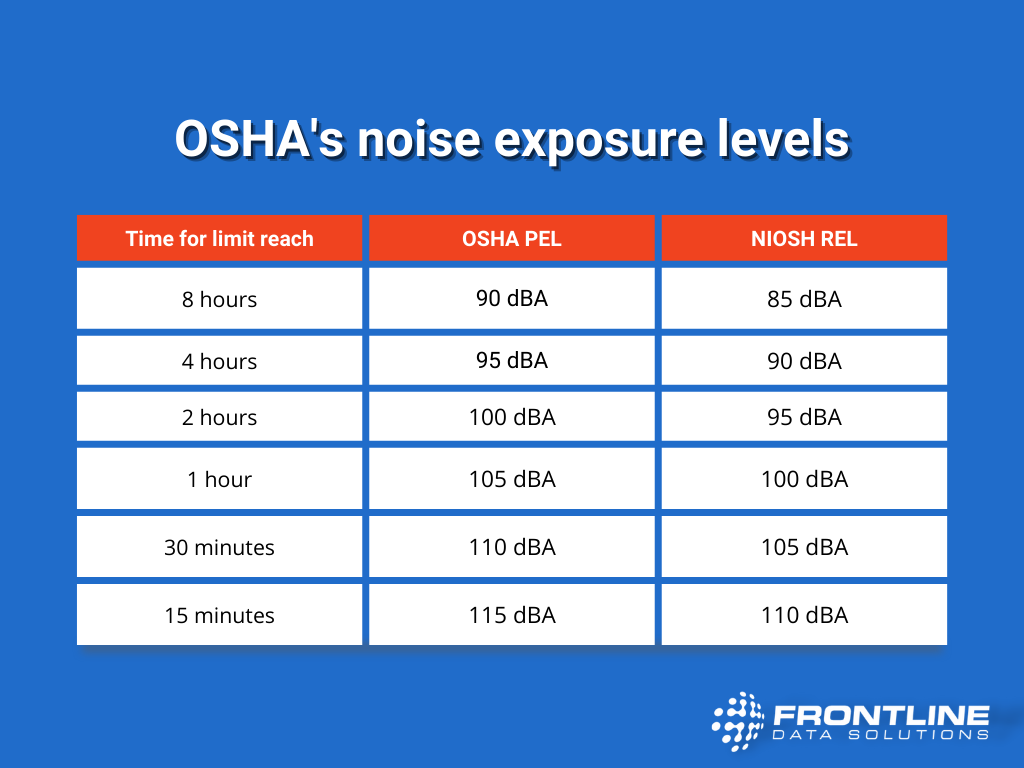
Image Source: Frontline Data Solutions
CDC data shows that workplace noise puts 22 million workers at risk of hearing damage each year. Proper noise protection protocols are the foundations of preventing permanent hearing damage.
Hearing Protection Devices
When noise levels reach or exceed 85 decibels over an 8-hour workday, OSHA requires employers to give workers free hearing protection. The core protection options include:
- Earplugs: Devices that fit snugly into ear canals, accessible to more people as formable foam, pre-formed, or custom-fitted
- Earmuffs: Devices that fully cover the outer ears, attached with a headband or hardhat
- Canal Caps: Devices that seal ear canal entrances with lightweight bands
Noise Level Monitoring
A systematic approach makes monitoring effective. Employers should start monitoring programs when worker exposure might reach or exceed 85 decibels. The monitoring program should:
- Design a Sampling Strategy to:
- Find employees who should be in hearing conservation
- Help choose the right hearing protectors
- Take continuous sound measurements from 80-130 decibels
Exposure Limits
NIOSH’s 30-year old recommended exposure limit stands at 85 A-weighted decibels for an eight-hour workday. Above this level:
- Employers must run ongoing hearing conservation programs
- Workers should get baseline audiograms within 30 days of their original exposure
- Yearly audiometric testing becomes required
- A retest within 30 days must confirm standard threshold shifts
Employers should assess how well hearing protectors work in their specific noise environments. Organizations can protect workers from noise-induced hearing loss through proper protocols and regular monitoring. Note that workplace noise-induced hearing loss is completely preventable by creating quieter workspaces.
Weather-Related Safety

Image Source: Perry Weather
Weather poses the most important risks to outdoor workers. Lightning strikes cause over 300 injuries and 50 fatalities each year in the United States. Teams can minimize weather-related incidents with proper safety protocols.
Heat Stress Prevention
Heat-related illnesses affect thousands of workers yearly but they’re completely preventable. Everything in prevention includes:
- Scheduling tasks during cooler hours
- Providing access to shaded areas
- Ensuring adequate hydration with water breaks
- Implementing acclimatization periods for new workers
Employers must monitor wet bulb globe temperature to protect workers. This gives the full picture of heat stress in direct sunlight. Workers must take mandatory cool-down periods every two hours once temperatures reach 85 decibels.
Cold Weather Protection
Cold environments just need systematic protection measures. These critical protocols include:
- Wearing three layers of loose-fitting clothing
- Protecting ears, face, hands, and feet
- Moving to warm locations during breaks
- Carrying extra clothing and emergency supplies
Wind chill creates extra risks. Exposed skin feels like it’s 11°F at 40°F with 35 mph winds. Employers must provide heated shelters when wind-chill temperatures drop to 20°F or below.
Lightning Safety
You must take immediate action when thunder strikes. These key guidelines include:
- Indoor Protection:
- Avoiding water contact
- Staying away from electrical equipment
- Keeping distance from windows and concrete
- Outdoor Precautions:
- Seeking shelter in enclosed buildings
- Maintaining 100-yard distance from water bodies
- Avoiding tall structures and metal objects
Organizations can boost workplace protection with automated weather alerting systems and clear emergency plans. These weather safety protocols help safeguard workers against environmental hazards while improving operational efficiency.
First Aid Fundamentals

Image Source: tradesafe
First aid readiness plays a key role in workplace safety. Studies show that treating serious injuries must start within 3-4 minutes after an accident to get the best results. Teams can handle medical emergencies until professional help arrives with proper training and preparation.
Simple First Aid Procedures
First aid includes immediate medical care given where injuries happen. The work to be done focuses on keeping the injured person stable through:
- Cleaning minor cuts and scrapes
- Treating minor burns
- Applying appropriate bandages
- Removing debris from eyes
- Managing heat stress by giving fluids
Emergency Response
Quick action is crucial during workplace medical emergencies. When someone finds an injured worker, authorized staff must:
- Check how serious the injury is
- Call emergency services if life is at risk
- Make the area safe to prevent more injuries
- Document the whole ordeal carefully
Organizations must build relationships with local ambulance services and keep medical staff available for consultation to respond better. On top of that, employers should set up nurse triage lines to check injuries and decide the right level of care.
First Aid Kit Requirements
OSHA requires specific supplies based on workplace hazard levels. Class A kits work for places with 40 or fewer employees in low-risk industries, while Class B kits suit high-risk sites like construction. Key items include:
- Gauze pads (minimum 4×4 inches)
- Two large gauze pads (8×10 inches)
- Adhesive bandages
- Gauze roller bandage
- Two triangular bandages
- Wound cleaning agents
- Simple tools (scissors, tweezers)
- Latex gloves
- Resuscitation equipment
Regular kit checks and supply refills help maintain compliance and emergency readiness. Companies can reduce injury effects and follow regulations by putting these first aid basics into practice.
Material Handling

Image Source: Safety Notes
Workplace injuries related to back problems make up one in five incidents, and 75% happen during lifting tasks. Organizations can reduce these incidents and keep operations running smoothly by using proper material handling practices.
Manual Lifting Safety
Workers need to prepare well to lift safely. Here’s what you need to check before any lift:
- Test load stability and weight
- Clear pathways of obstacles
- Secure proper footwear
- Position loads between knees and shoulders
You can protect yourself best by keeping three-point contact during lifts – two hands and one foot, or two feet and one hand. Workers should ask for help when loads are:
- Too bulky to grasp properly
- Block forward vision
- Feel too heavy to handle comfortably
Mechanical Aid Usage
Using mechanical equipment reduces physical strain by a lot. These helpful tools include:
- Hand trucks for bulky objects
- Platform trucks for irregular shapes
- Semi-live skids for temporary storage
- Rolling conveyors for continuous movement
Workers should check these points before using any mechanical aid:
- Equipment maintenance status
- Weight capacity limits
- Proper wheel condition
- Platform integrity
Storage Requirements
Smart storage practices prevent accidents and keep materials easy to access. Storage areas must meet these standards:
- Environmental Controls:
- Protection from rain and flooding
- Adequate ventilation systems
- Proper foundation support
- Sufficient aisle space
- Material Organization:
- Store heavy items between knee and shoulder level
- Place lighter materials on upper shelves
- Maintain 18-inch clearance from sprinkler heads
- Secure storage racks firmly to prevent collapse
Storage areas must stay clear of materials that could cause trips, fires, or attract pests. On top of that, items stored in tiers like bags, containers, and bundles need proper stacking, blocking, and interlocking to stay secure. Organizations can minimize material handling risks and keep the workplace safe by following these guidelines consistently.
Welding and Cutting Safety

Image Source: Illustra Pro
Welding operations just need careful attention to safety protocols. Equipment misuse and poor work practices can cause fires, explosions, severe skin burns and eye damage.
Hot Work Permits
Hot work permits are mandatory for welding operations outside designated areas. These permits must specify roles, fire prevention measures and emergency procedures. The permits expire at 3:00 p.m. on regular workdays unless there’s an emergency.
PPE Requirements
Required protective gear includes:
- Fire-resistant head coverings under welding helmets
- Gauntlet-type leather gloves to protect wrists and forearms
- Dark-colored, long-sleeved shirts with buttoned cuffs
- Fully laced high-top boots that prevent spark entry
Fire Watch Procedures
Fire watchers must stay alert when welding happens within 35 feet of combustible materials. Their duties include:
- Keeping fire extinguishing equipment ready
- Knowing facility alarm systems
- Watching exposed areas for at least 30 minutes after operation
- Using extinguishing equipment only within its capacity
Storage Requirements
Oxygen cylinders must be kept away from fuel-gas cylinders by at least 20 feet or behind 5-foot high fire-resistant barriers. Cylinders need storage in well-ventilated, dry spots away from elevators, stairs and gangways.
Handling Procedures
Operators must place vent systems close to arcs when welding stainless steel materials. Surface preparation is vital and requires proper cleaning with wire brushes, sandblasting and chemical treatments.
Emergency Response
Medical departments should see workers right away if they suffer eye or skin injuries. Chemical exposures require documented spill response procedures and evacuation protocols when needed.
Daily Cleaning Procedures
Regular maintenance includes:
- Cleaning nozzles with welding pliers
- Checking contact tips for debris
- Using filtered compressed air to remove liner debris
- Securing work clamp leads and gun cables
Waste Management
Environmental protection depends on proper welding waste disposal. This covers electrode stubs, wire loss during metal inert gas welding and material recycling. Organizations can minimize welding-related incidents and meet regulatory requirements by following these safety protocols systematically.
Comparison Table
Safety Topic | Primary Hazards/Risks | Key Safety Requirements | Essential Equipment/PPE | Inspection/Maintenance Requirements | Training/Certification Needs |
---|---|---|---|---|---|
PPE | Workplace hazards, contamination risks | Must fit properly and meet ANSI standards | Varies by hazard type | Regular checks before use, scheduled maintenance | Not mentioned |
Fall Protection | Falls from heights (>10ft) that cause serious injury or death | Load must be 5,000 lbs minimum per user | Body harnesses, safety nets, guardrails | Checks before each workshift, yearly inspection by Competent Person | Annual inspection records needed |
Electrical Safety | Death, shock events, burns | Power must be off before work starts, LOTO procedures | Insulated tools, GFIs, double-insulated power tools | Tools need regular checks, proper ground testing | LOTO needs authorization |
Fire Safety | Property damage, injuries, death | Clear escape routes, meeting points | Fire extinguishers (A-B-C types), sprinkler systems | Fire protection equipment needs regular checks | Training for evacuation wardens |
Hazardous Materials | Health and environmental risks | Safe storage, labels, air flow | Level A-D PPE based on risk | Regular chemical inventory verification | Staff must know handling steps |
Machine Guarding | Amputations, crushing injuries, death | Guards must block access to dangerous parts | Fixed, interlocked, adjustable guards | Regular checks of mounts and guard condition | Not mentioned |
Ladder Safety | Falls, injuries, death | Position must follow 1:4 ratio rule | Type I-III ladders based on duty rating | Structure needs regular inspection | Not mentioned |
Confined Space | Dangerous air quality, engulfment | Entry permit required, air testing | Full-body harness, gas monitors, ventilation systems | Air quality needs constant monitoring | Permit documentation required |
Ergonomics | Musculoskeletal disorders | Correct desk setup, regular breaks | Adjustable chairs, keyboard trays | Workplace needs regular assessment | Training on proper posture |
Hand/Power Tools | Injuries cost $15.40M yearly | Tools must match specific tasks | Single/double-handled tools with specific sizes | Daily upkeep, scheduled recalibration | Training required at hire |