The 1960s saw a devastating toll of 14,000 worker deaths each year because workplace safety wasn’t regulated properly.
This loss of life sparked the creation of OSHA in 1970. OSHA now monitors more than 11 million worksites throughout the United States. Workplace safety remains a major concern, especially regarding fire hazards. Commercial property fires result in more than $2.4 billion worth of damage each year. The situation becomes more alarming since 52% of major fires happen in buildings that lack working smoke detectors.
Our team has identified the most common OSHA safety violations that businesses face. These violations can lead to fines up to $161,323 for each case and potentially force your business to close. Understanding these violations is a vital part of business operations – it goes beyond avoiding penalties to protect your workers’ lives.
Blocked Emergency Exits: A Critical Life Safety Violation

Image Source: Safe and Sound Security
Emergency exits are critical lifelines when workplace disasters strike. OSHA inspectors often find these vital escape routes blocked or locked. A shocking example emerged at a national retail chain where inspectors found emergency exit doors secured with bike locks while employees worked inside.
Common Exit Blockage Issues
Exit pathways get blocked by merchandise, equipment, and storage materials. OSHA teams regularly spot boxes, rolling carts, portable ladders, and powered industrial trucks blocking emergency routes. Some facilities make things worse by using locks, chains, or boards to secure emergency doors that need special tools or knowledge to open.
OSHA Requirements for Exit Routes
Workplaces must have at least two designated exit routes so people can evacuate quickly. These paths must stay clear and be at least 28 inches wide. The routes need good lighting and clear signs that say “Exit”. Any door that looks like it might be an exit must have a “Not an Exit” sign or show what it’s really used for.
Financial Penalties for Non-Compliance
Companies pay heavily for exit violations. A retailer had to pay USD 435,081 for blocked emergency routes and locked exits. Another business got hit with USD 227,304 in fines after OSHA found blocked exit paths in storage areas. A single retail chain has paid more than USD 15 million in fines over the last several years for safety violations, including blocked exits.
Prevention and Best Practices
To keep exit routes compliant:
- Clear exit paths of boxes, equipment, and storage materials
- Keep doors unlocked from inside at all times
- Install proper lighting along exit routes
- Use fire-resistant materials to separate exits from other areas
- Check exit pathways regularly
Fire retardant materials need renewal to maintain their protective properties. Exit routes must stay maintained even during construction, repairs, or building changes.
Inadequate Fire Protection Systems
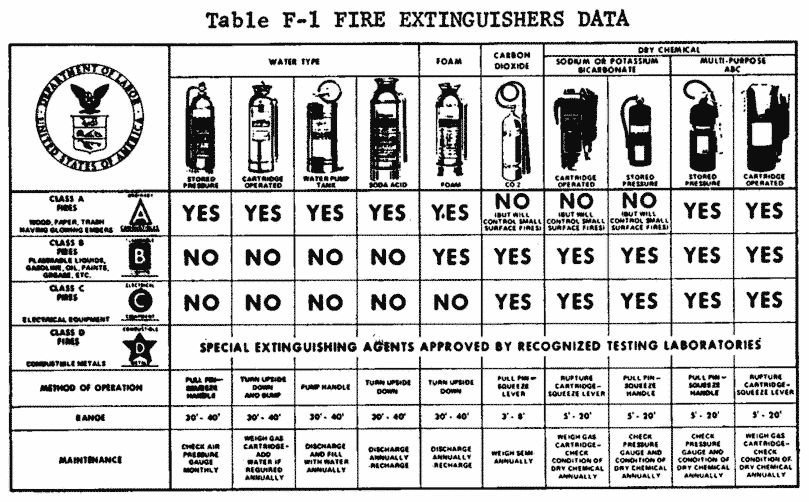
Image Source: OSHA
Fire protection systems serve as your first defense against workplace fires. OSHA inspections show that 65% of businesses don’t maintain these life-saving systems properly.
Required Fire Safety Equipment
OSHA requires a complete fire protection setup that has sprinkler systems, fire extinguishers, and alarm devices. You must place a minimum-rated 10B fire extinguisher within 50 feet of areas that use more than 5 gallons of flammable liquids. On top of that, it’s mandatory to install automatic sprinkler systems during construction and keep them working through any building changes.
Maintenance and Testing Schedules
Your system’s reliability depends on regular maintenance. Sprinkler systems just need quarterly and annual inspections. Here’s what you should check:
- Weekly: Control valves and dry/deluge system gages
- Monthly: Wet pipe system gages and alarm valves
- Quarterly: Alarm devices and hydraulic nameplate verification
- Annual: Certified professionals must do a full system check
Common System Failures
Poor maintenance and oversight lead to most system failures. Corrosion in wet pipe systems can seriously damage system integrity, especially when you have leaks or total system breakdown. Your system can also fail from mechanical damage during construction or renovations. Cold weather brings its own risks – water-filled pipes might burst in freezing temperatures.
Compliance Documentation
OSHA wants detailed records of all fire protection systems. Your company must keep written fire prevention plans that employees can access easily. These plans must list:
- Major fire hazards
- Proper handling procedures for hazardous materials
- Control measures for potential ignition sources
- Equipment maintenance schedules
Companies with more than 10 employees must keep written documentation – it’s not optional. You need to keep all inspection records until your next annual maintenance. Regular updates to these documents help you stay compliant with changing safety standards and regulations.
Hazardous Material Storage Violations
Image Source: North Carolina Department of Public Safety
Safety concerns about hazardous material storage remain critical since poor handling can result in serious OSHA violations and workplace accidents. Recent inspections show chemical storage violations have resulted in penalties of USD 484,401.
OSHA Chemical Storage Guidelines
OSHA requires flammable liquids to be stored in approved containers and cabinets. Storage rooms can only have 25 gallons of flammable liquids outside approved cabinets. Facilities must use specially constructed storage cabinets when quantities go beyond this limit. These cabinets need:
- Exterior grade plywood (minimum 1-inch thickness)
- Fire-resistant materials
- Clear labeling stating “Flammable-Keep Away from Open Flames”
Common Storage Mistakes
Regular inspections reveal that problems are systemic in chemical storage practices. The biggest problems include:
- Storing incompatible materials together
- Insufficient aisle space between chemical drums
- Improper stacking of containers causing structural stress
- Placing flammable materials near ignition sources
Required Safety Documentation
Safety documentation is the life-blood of compliance. Each facility must keep:
- Written hazard communication program
- Complete chemical inventory list
- Safety Data Sheets (SDS) for each hazardous substance
- Detailed emergency response procedures
Employee Training Requirements
Workers who handle hazardous materials must complete a thorough training program. The original training should happen within 90 days of employment. The program includes:
- General awareness and familiarization
- Function-specific procedures
- Safety protocols
- Security awareness
- Emergency response procedures
Companies must keep training records for three years with the employee’s name, completion date, materials used, and trainer information. Facilities that store more than 60 gallons of flammable liquids must have at least one portable fire extinguisher rated 20-B units within 10 feet of storage room doors.
Storage rooms just need specific construction that meets fire-resistance ratings. Materials that react with water need separate storage areas to prevent dangerous interactions. Outside storage areas should maintain 12-foot-wide access ways within 200 feet of container piles, among other proper grading or containment measures to control potential spills.
Electrical Safety Non-Compliance

Image Source: HAZWOPER OSHA Training
One workplace fatality happens each day due to electrical hazards. This makes electrical safety compliance crucial for businesses. OSHA data shows most workplace electrocutions happen because of unsafe equipment installations and dangerous work practices.
Wiring and Circuit Violations
Businesses face OSHA citations under Sections 1910.303 and 1910.305 for electrical violations. Missing outlet covers, improperly closed circuit breaker panels, and exposed live wires top the list of common violations. Proper wiring maintenance is crucial since electrical malfunctions cause 22% of uncontained fires in facilities.
Extension Cord Misuse
Safety protocols for flexible cords are specific. OSHA rules state that extension cords must meet these requirements:
- Rated for hard or extra-hard usage
- Three-wire type for proper grounding
- Free from cuts, frays, or exposed wiring
- Protected when running through doorways
Inspectors often find cords fastened with staples, hung incorrectly, or used as permanent wiring solutions.
Required Safety Measures
Equipment work should be done by qualified personnel who can identify energized parts and understand approach distances. Key safety protocols include:
- De-energizing circuits prior to maintenance
- Using lockout devices to prevent energization
- Verifying power disconnection with AC voltage testers
- Implementing proper grounding procedures
Inspection Protocols
OSHA’s equipment inspection requirements focus on:
- Visual examination of cord-connected equipment before each shift
- Immediate removal of defective items from service
- Regular testing of ground-fault circuit protection
- Documentation of all electrical safety procedures
Circuits above 600 volts need testing equipment verification right before and after use. Breaking these protocols can lead to penalties up to USD 15,000 per incident. Criminal charges may apply for willful non-compliance.
Faulty Emergency Lighting

Image Source: Lighting Inverter Supply
Emergency lighting plays a critical role during power outages. Yet OSHA inspections show that more than two-thirds of businesses don’t test their emergency lighting systems yearly.
OSHA Emergency Lighting Standards
Buildings with artificial lighting must have adequate illumination for all exit facilities, according to OSHA. The word “Exit” must appear in clear, readable letters. These letters should be at least six inches high, and their main strokes must be three-fourths of an inch wide. Beyond OSHA rules, facilities need to follow NFPA 101 Life Safety Code. This code requires emergency lights to work for at least 90 minutes after power goes out.
Testing Requirements
Monthly inspections are the life-blood of emergency lighting maintenance. NFPA code suggests:
- Monthly tests lasting 30 seconds to check required lighting
- Yearly tests running 90 minutes to mimic long outages
Self-testing systems need visual checks every 30 days to spot any damage. Systems with computer controls create test reports automatically, which removes the need for manual records.
Common Maintenance Issues
Battery problems cause most emergency lighting failures. Other typical problems include:
- Backup batteries that are dead or broken
- Burnt-out bulbs that reduce system reliability
- Lights placed wrongly against OSHA rules
- Too much dust that hurts performance
Compliance Solutions
Your emergency lighting systems will stay compliant when you:
- Set up regular tests that follow NFPA guidelines
- Keep detailed records of all maintenance work
- Switch out bad batteries and bulbs right away
- Put lights in correct spots near exits and stairs
Breaking these rules can lead to heavy fines – up to £400,000 in the worst cases. Safety labs test certified emergency lighting equipment for fire and shock risks. Good record-keeping matters because building inspectors often want to see your testing history.
Fire Door Violations

Image Source: Alliance Environmental Group
Recent inspections show that all but one of these fire doors in over 100,000 cases failed simple safety standards. This highlights a major workplace safety concern.
Fire Door Requirements
Fire doors just need specific construction with fire-resistant materials and proper certification from OSHA-recognized testing laboratories. A certification label must be displayed on each door to show its fire rating, which typically ranges from 20 to 180 minutes of fire resistance. The door unit’s assembly has the frame, hardware, and self-closing mechanisms that contain fires within designated areas.
Common Compliance Issues
Door effectiveness gets compromised by critical violations that inspectors often find. The biggest problems are:
- Door components’ damage affecting structural integrity
- Wrong installation causing misalignment
- Missing or broken intumescent seals vital for fire containment
- Wrong clearance between door and frame
The excessive clearance near latch areas creates major risks that could cause latch disengagement during fires. Unauthorized modifications like drilling holes without proper repairs create weak points where fire could spread.
Maintenance Protocols
NFPA 80 requires yearly inspections by qualified personnel. The work to be done includes:
- Checking if self-closing mechanisms work properly
- Making sure latches engage securely
- Looking at door alignment and hardware condition
- Testing fusible link systems connected to warning devices
Documentation Needs
Complete record-keeping is vital for compliance. Required documentation has:
- Yearly inspection reports with qualified personnel’s signatures
- Detailed maintenance records of repairs and modifications
- Door inventory with locations, types, and fire ratings
- Certification labels proving OSHA compliance
Facilities must keep these records ready for authorities with jurisdiction. On top of that, listing agencies must approve and document any modifications to maintain certification. Fire ratings become invalid with unauthorized changes, which could lead to OSHA violations with penalties up to USD 156,259 per incident.
Improper Fire Extinguisher Maintenance
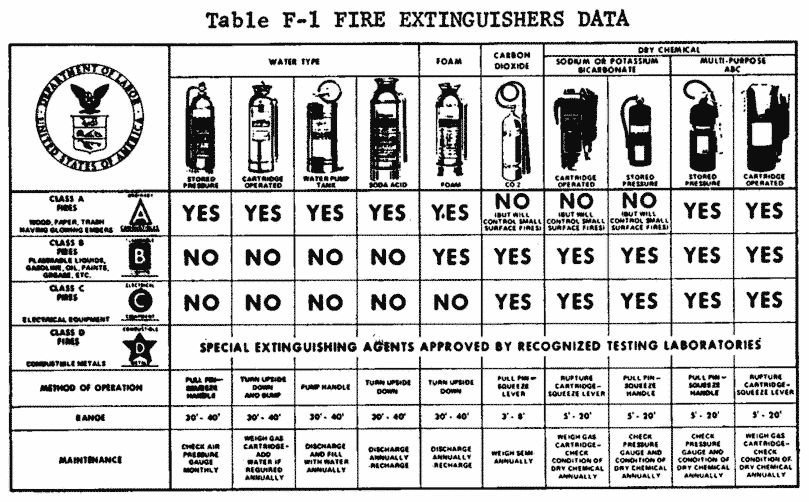
Image Source: OSHA
Recent OSHA data shows that retail businesses face fines of over USD 500,000 each year due to fire extinguisher violations. Poor maintenance and wrong placement of vital firefighting equipment cause these violations.
Inspection Requirements
Monthly visual inspections are the foundations of good fire extinguisher maintenance. Each inspection must check:
- Equipment placement in designated spots
- Pressure gage readings to confirm full charge
- Signs of damage or corrosion on the unit
- Clear and unblocked nozzles
Stored pressure extinguishers need yearly maintenance checks. Dry chemical units need detailed evaluation every six years. Units must undergo hydrostatic testing after 12 years of service.
Location and Accessibility Issues
Employee travel distance to fire extinguishers should not exceed 75 feet. Units must be mounted according to these rules:
- Units under 40 pounds should be no higher than 5 feet from the floor
- Ground clearance must be at least 4 inches
- Location must be clearly visible or marked with proper signs
Training Requirements
Workers must complete fire extinguisher training when hired and take yearly refresher courses. The training program should cover:
- Basic principles of extinguisher operation
- Risks of fighting fires in their early stages
- How to pick the right equipment based on fire type
- Steps in the emergency action plan
Record Keeping
Proper documentation is a vital part of compliance. Employers should keep:
- One year’s worth of annual maintenance records
- Monthly inspection logs through tags or digital systems
- Training certificates for staff assigned to firefighting duties
Internal examinations need verification-of-service collars that show:
- When maintenance was done (month and year)
- Who did the service
- What maintenance work was completed
Missing proper documentation can result in fines averaging USD 19,000 per violation. Insurance companies might also reject claims if maintenance records are incomplete or missing.
Missing or Inadequate Safety Signage

Image Source: Atlas Insurance
Workplace safety sign violations are the second most common infraction, resulting in $16,131 penalties per case. A detailed analysis shows poor hazard communication through signs ranks as the third leading cause of workplace injuries.
Required Safety Signs
OSHA groups safety signs into specific categories based on how severe the hazard is. Danger signs use white letters on red backgrounds to show immediate hazards that require special precautions. Warning signs come in orange and alert workers about risks of death or serious injury. Caution signs have yellow backgrounds with black panels to warn workers about unsafe practices.
Placement Guidelines
Workers must see the signs during all operations near potential hazards. Signal words like “DANGER” or “CAUTION” should be readable from at least five feet away according to OSHA rules. Signs work best when they have:
- Rounded or blunt corners without sharp edges
- Good visibility in work areas
- Proper lighting in dark conditions
- Strategic spots near known hazards
Multi-Language Requirements
OSHA doesn’t strictly require multilingual signs, but strongly encourages employers to post Spanish notices if they have Spanish-speaking workers. Research suggests workers who don’t speak English well face higher risks of injury. ANSI Z535.3-2002 standards support using safety symbols with text to help bridge language gaps.
Regular Inspections
Regular sign checks help maintain compliance. Essential inspection tasks include:
- Checking if signs are visible and readable
- Looking for damage or fading
- Testing proper lighting
- Making sure hazards are correctly shown
Damaged, faded or hard-to-read signs should be replaced right away. Companies must keep records of where signs are placed, what types they use, and when they inspect them. Regular checks help identify areas that just need more visual warnings or updated hazard signs.
Sprinkler System Violations

Image Source: Alliance Environmental Group
Properly managed sprinkler systems reduce fire-related deaths by 90%, yet system failures still cause significant property damage. OSHA just needs detailed sprinkler system compliance to keep workplaces safe.
System Requirements
Your workplace’s automatic sprinkler systems must provide water flow patterns that cover the entire space. Everything in the system includes:
- Automatic water supply that runs for 30-minute design flow
- Local waterflow alarms when systems have more than 20 sprinklers
- 18-inch minimum vertical clearance between sprinklers and materials
Common Compliance Issues
Problems are systemic with blocked sprinkler heads and poor maintenance. Sprinkler heads won’t work when objects block them, and materials within 18 inches of sprinkler heads block effective coverage. You should watch for these critical issues:
- Wrong system selection for building needs
- Wet pipe system’s corrosion affecting integrity
- Mechanical damage during renovations
Maintenance Schedules
NFPA 25 sets the baseline for how often you should check your systems. Control valve inspections and gage monitoring happen weekly. Your monthly checklist should include:
- Gage inspection for operational status
- Water pressure verification
- Sprinkler clearance assessment
- Equipment condition evaluation
Testing Protocols
You just need certified professionals to do a detailed evaluation yearly. Different systems have specific testing schedules:
- Full-flow trip tests happen every 3 years for dry-type systems
- Gages need replacement or testing every 5 years
- Internal inspection of check valves happens every 5 years
- Fast response elements get tested every 10 years
Your facility must keep detailed records of all inspections and tests. Systems installed before January 1981 can follow the National Fire Protection Association standards from their installation time. The right acceptance tests cover flushing underground connections, hydrostatic piping tests, and drainage facility checks.
Inadequate Emergency Action Plans
Image Source: OSHA
A detailed emergency action plan (EAP) is the life-blood of workplace safety. OSHA investigations show many facilities have critical gaps in their preparedness. A tragic warehouse ordeal led OSHA to identify three major problems: emergency equipment was not available, employees lacked proper training, and location-specific planning fell short.
Required Plan Elements
Every EAP must meet specific OSHA requirements. Your plan should clearly spell out procedures to report emergencies, evacuation protocols, and how to manage critical operations. Written documentation becomes mandatory if you have more than 10 employees. These plans must cover:
- Emergency reporting mechanisms
- Evacuation routes and assignments
- Procedures for employees managing critical operations
- Methods to account for all personnel
- Rescue and medical duties
- Emergency coordinator contact information
Employee Training
The original training sets the foundations of emergency preparedness. The core team must go through the EAP with staff members in these situations:
- Job responsibilities change
- Plan modifications occur
- New assignments begin
Documentation Requirements
OSHA compliance depends on proper record-keeping. Your organization must keep:
- Written emergency procedures
- Training completion records
- Equipment maintenance logs
- Regular drill documentation
Regular Updates and Reviews
Workplace conditions change constantly, so EAPs just need periodic evaluation. A full picture of your preparedness comes from “what-if” analyzes and job hazard assessments. Your emergency plans require annual testing through drills and exercises. On top of that, you should bring in community emergency responders during exercises to improve coordination.
Recent OSHA citations prove why proper emergency planning matters. One employer paid USD 223,525 in penalties because their emergency procedures fell short. A current, well-documented emergency action plan and regular training sessions will give a workplace both safety and OSHA compliance.
Comparison Table
Violation Type | Main OSHA Requirements | Common Violations | Inspection/Maintenance Frequency | Typical Penalties | Required Documentation |
---|---|---|---|---|---|
Blocked Emergency Exits | Paths must be 28″ wide, 2 exit routes needed in workplace | Items and equipment block paths; doors are locked/chained | Regular inspections needed | Up to $435,081 | Exit route compliance records |
Inadequate Fire Protection | Complete fire protection systems; 10B extinguishers within 50ft | 65% of businesses don’t maintain properly | Weekly, Monthly, Quarterly, Annual checks | Not specified | Written fire prevention plans, inspection records |
Hazardous Material Storage | 25-gallon limit outside approved cabinets; specific cabinet requirements | Materials stored incorrectly; narrow aisles | Not specified | $484,401 | Chemical inventory, SDS sheets, emergency procedures |
Electrical Safety | Equipment work limited to qualified staff; proper grounding needed | Wires exposed, outlet covers missing, cords used wrong | Equipment checks before each shift | Up to $15,000 per incident | Electrical safety procedures, inspection records |
Faulty Emergency Lighting | Exit signs need 6″ high letters; 90-min backup power | Dead batteries, burnt bulbs, wrong positioning | Monthly 30-sec tests; Annual 90-min tests | Up to £400,000 | Testing and maintenance records |
Fire Door Violations | Fire-resistant build; certified labels required | Parts damaged, wrong installation, seals missing | Annual inspections | Up to $156,259 per incident | Inspection reports, maintenance records, door inventory |
Improper Fire Extinguisher | Units must be within 75ft; proper mounting height | Wrong placement, poor maintenance | Monthly visual checks; Annual maintenance | $19,000 per violation | Maintenance records, training certificates |
Missing Safety Signage | Color codes required; 5ft minimum readability | Signs damaged/faded, wrong placement | Regular inspections needed | $16,131 per incident | Sign locations, types, inspection records |
Sprinkler System | 18″ clearance under heads; 30-min water supply | Heads blocked, poor maintenance | Weekly, Monthly, Annual checks | Not specified | Inspection and test documentation |
Emergency Action Plans | Written plans if 10+ employees; specific steps needed | Equipment not available, training gaps | Annual drill testing | Up to $223,525 | Written procedures, training records, drill documentation |
Conclusion
Safety violations at work create risks that go way beyond just paying fines. Each violation puts employees’ lives at risk and threatens business operations. Fire safety rules don’t deal very well with just one system – they need everything from clear exit paths to working sprinklers and emergency lights.
Companies must focus on checking their safety systems regularly. They need proper paperwork and staff training. A single missed violation like blocked exits or broken fire doors could spell disaster in an emergency.
OSHA compliance saves lives and protects businesses. Fines can reach $435,081 for each incident, which shows how serious these violations are. Smart business owners know that investing in safety measures costs nowhere near as much as fixing violations later.
Fire safety at work needs constant watchfulness. System checks, proper documentation, and quick fixes for problems help keep everyone safe while following OSHA rules. Note that prevention through good maintenance and training works better than reacting to emergencies.
FAQs
Employers who violate OSHA safety standards can face significant consequences, including substantial fines of up to $161,323 per incident. Additionally, repeated or willful violations may result in criminal charges. Most importantly, unsafe working conditions put employees’ lives at risk and can lead to workplace accidents, injuries, and fatalities.
No, it is illegal for an employer to fire, demote, transfer, or retaliate in any way against an employee for reporting safety violations to OSHA. This is considered whistleblower retaliation and is protected under federal law. Employees who experience such retaliation can file a complaint with OSHA or the Department of Labor.
Employees who notice safety hazards should first report their concerns to their supervisor or employer in writing. If the employer fails to address the issue, employees have the right to file a confidential complaint with OSHA. It’s important to document all safety concerns and communications with management regarding these issues.
Fire safety equipment should be inspected and maintained regularly. Fire extinguishers require monthly visual inspections and annual maintenance checks. Sprinkler systems need weekly, monthly, and annual inspections depending on the components. Emergency lighting should undergo monthly 30-second tests and annual 90-minute tests. Adhering to these schedules is crucial for ensuring the effectiveness of fire safety systems.
Common OSHA violations related to emergency exits include blocked exit routes, locked or chained emergency doors, inadequate exit signage, and insufficient lighting along exit pathways. OSHA requires that exit routes remain unobstructed, properly lit, and clearly marked at all times. Employers must ensure at least two exit routes are available in most workplaces and that these routes meet specific width and design requirements.