Daily five-minute safety discussions can provide your employees with over 20 hours of vital safety education yearly. This simple practice creates the difference between a safe workplace and one where accidents happen.
Companies that hold regular safety meetings report fewer workplace injuries consistently. The biggest problem lies in making these meetings work and keeping people involved. Safety topics continue to expand – ranging from deadly electrical hazards at construction sites to workplace violence threats in healthcare settings.
Common workplace hazards like slips and falls remain a leading cause of injuries. New threats such as phishing attacks increase each year. Selecting the right safety topics has become more significant than ever. Our detailed list of 47 safety meeting topics will help keep your workers alert and involved throughout 2025.
Physical Safety Fundamentals

Image Source: The HIPAA Journal
Physical hazards create big risks in workplaces that damage tissue when energy transfers from dangerous sources to workers. Everything in workplace safety depends on understanding these basics.
Common Physical Hazards Workplace noise levels raise serious concerns, especially when you have emergency departments where levels hit 61-69 decibels. Some intensive care units show readings above 100 decibels. Workers face risks from extreme temperatures that can lead to heat stress, frostbite, or hypothermia. Electrical exposure brings equal danger with severe burns, shocks, or deadly electrocution.
Prevention Strategies Safety teams should spot and fix hazards before anyone gets hurt. Companies must use a hierarchy of controls that starts with engineering solutions. Safe work practices, administrative controls, and protective equipment follow in order. Companies should also keep their protocols current to monitor, report, and respond to physical hazards.
Training Requirements OSHA sets specific training schedules for safety topics. To cite an instance, new hires need fire extinguisher training and yearly refreshers. Workers must complete noise exposure training if levels go above 90 decibels during an 8-hour shift. Respirator training needs yearly updates that reflect workplace changes.
Real-life Examples Two young workers aged 14 and 19 lost their lives at a grain storage facility. The whole ordeal happened while they walked down corn in a grain bin. Their employer didn’t give them safety harnesses or turn off grain-moving equipment. Another tragic case involved an 18-year-old worker who died in a portable mortar mixer at a construction site. The accident happened because proper lockout steps weren’t followed during cleaning. A 20-year-old carpenter’s story adds to these tragedies. He suffered severe brain injuries after falling through a second-story stairway opening without proper fall protection.
These stories show why proper safety protocols, training, and protective equipment matter in stopping workplace accidents. Employers must follow safety standards and watch workplace conditions closely.
Electrical Safety Protocol

Image Source: HAZWOPER OSHA Training
Electrical accidents take nearly 1,000 lives each year in the United States, while at least 30,000 non-fatal shock incidents occur annually. Safety meetings must emphasize proper electrical safety protocols to protect workers.
Identifying Electrical Hazards
The construction sector bears the highest risk and accounts for 52% of all electrical fatalities. Damaged equipment, frayed cables, and improper grounding pose common threats. Workers should watch for exposed electrical components, including temporary lighting and open power distribution units that might cause shocks and burns.
Safe Work Practices
Electrical installations and equipment should match their intended use and operating conditions. Qualified technicians must verify that circuits have no power before work begins. Workers should stay at least 10 feet away from overhead power lines.
Essential safety practices include:
- Using properly rated fuses and circuit-breakers for each circuit
- Keeping isolators and fuse-box cases closed and locked
- Making sure cables and fittings can withstand the work environment
- Installing easy-to-reach emergency switches for quick power cutoff
Equipment inspections play a significant role. Equipment showing damaged plugs, loose cables, or burn marks that indicate overheating should be taken out of service right away. Equipment used in wet or dusty environments needs more frequent inspections.
Emergency Response
Quick action can save lives during electrical emergencies. The power source must be shut off immediately if someone gets shocked. No one should touch the victim until they’re free from the electrical source. Use non-conductive objects such as dry wooden boards or rubber electrical cords to break contact with the circuit.
Check for breathing and pulse once the scene becomes safe. Start CPR and use an AED if needed. Medical attention becomes necessary even for minor shocks because heart complications can develop up to 24 hours after exposure.
Safety meetings should stress that all electrical work requires proper lockout/tagout procedures. People without proper training should keep their distance from energized equipment. Only qualified personnel should handle electrical repairs.
Fire Safety and Prevention

Image Source: reliablefire.com
Fire safety protocols are the life-blood of workplace security. U.S. fire departments respond to emergencies every 23 seconds in 2021. Office and store fires caused $932 million in direct property damage in 2020.
Fire Risk Assessment
A systematic assessment of fire hazards helps maintain workplace safety. Start by identifying potential ignition sources, flammable materials, and people at risk. The next step involves checking emergency routes, fire detection systems, and firefighting equipment placement. You need regular reviews, especially after workplace changes like new equipment installation or staff updates.
Emergency Evacuation Procedures
Workers must stop all activities when they hear the fire alarm. Department safety wardens need to ensure everyone evacuates, and they should pay special attention to people with mobility limitations. The basic protocols include:
- Using stairs exclusively, never elevators
- Moving at least 150 feet away from the building
- Assembling at designated evacuation points
- Awaiting official “all clear” before re-entry
Fire Extinguisher Types
There are five main types of fire extinguishers, each designed for specific fires:
Class A: Works against ordinary materials like cloth, wood, and paper. You’ll find these in homes and businesses.
Class B: Made for flammable liquids including grease, gasoline, and oil-based paints.
Class C: Handles electrical equipment fires with non-conductive agents.
Class D: Works on flammable metals, commonly found in factories.
Class K: Designed for kitchen fires with vegetable oils, animal fats, and cooking appliances.
The quickest way to ensure safety is to choose multipurpose extinguishers labeled “B-C” or “A-B-C” that help curb most workplace fires. Look for the “UL Listed” or “ULC Listed” certification to ensure reliability. Training is vital – employees should receive instruction when hired and take annual refresher courses. The PASS system (Pull, Aim, Squeeze, Sweep) is the basic technique to operate fire extinguishers.
Personal Protective Equipment (PPE)

Image Source: Stop-Painting.com Blog – We are your Floor Tape & Pavement Tape …
Personal protective equipment stands as your last line of defense against workplace hazards. The right selection and upkeep of PPE plays a vital role in worker safety. OSHA data shows that poor PPE leads to over 1,000 workplace injuries each year.
Essential PPE Components
Your exposure risks determine what protective gear you need. Head protection must meet ANSI Z89.1-2009 standards. Protective footwear needs to follow ASTM F-2412-2005 specifications. Here’s what you need:
- Safety glasses and goggles to protect your eyes
- Hard hats to protect your head
- Steel-toed boots to keep feet safe
- Chemical-resistant gloves to guard hands
- Respirators to handle airborne hazards
- Hearing protection devices to block harmful noise
Proper Usage Guidelines
Employers should train their workers really well on PPE usage. OSHA rules say training must cover how to select gear, fit it properly, and know its limits. Workers need to show they understand these concepts in their native language before they start any work that needs PPE.
You should follow these steps to stay protected:
- Look over your equipment before each use
- Make sure everything fits right
- Take off dirty PPE before leaving work areas
- Switch out damaged items right away
- Stick to what the manufacturer says
Maintenance Tips
Good care makes your equipment last longer and work better. Studies show that poor maintenance causes 65% of PPE failures. Here’s how to take care of your gear:
Daily Care: Clean your hardhat with warm water and soap. Let it dry naturally. Keep protective gear away from sunlight and extreme temperatures.
Regular Inspection: Look for holes or thin spots in gloves. Check if your eyewear has cracks, warping, or scratches that block vision. Make sure shoe soles give you good traction.
Storage Requirements: Keep your PPE in original sealed packages until you need it. Store everything away from your regular clothes and keep it clear of chemicals, high humidity, or anything that could contaminate it.
A complete PPE program forms the foundation of workplace safety meetings. The right selection, proper use, and good maintenance of PPE cuts down injury risks by a lot while meeting all regulations.
Ergonomic Safety

Image Source: Cary Orthopedics
Musculoskeletal disorders make up almost 30% of worker injury cases. This makes ergonomic safety a vital topic in workplace discussions. Companies that implement ergonomic principles properly report fewer workplace injuries and improved productivity.
Workstation Setup
Your desk setup plays a fundamental role in preventing strain. The computer monitor should sit directly in front of you, about an arm’s length away. Place the keyboard so the ‘B’ key lines up with your belly button. Make sure you have enough leg room under the desk. Don’t store items that could limit your movement.
Proper Posture
The right posture helps prevent back pain and muscle fatigue. Your back should rest straight against the chair’s backrest while your buttocks press firmly against the seat. Keep your thighs parallel to the floor and feet flat on the ground or on a footrest. Your arms work best with elbows at 90 degrees and relaxed shoulders.
Movement Breaks
Studies show that active breaks between sitting periods lower cardiac risk and plasma glucose levels substantially. You should take quick 3-5 minute breaks every half hour. During these breaks:
- Get up and walk around
- Do gentle stretches
- Look at distant objects to rest your eyes
- Switch between sitting and standing
Equipment Adjustments
The right equipment setup helps prevent musculoskeletal disorders. Set your chair height to keep thighs parallel to the floor. The monitor’s top third should match your eye level when seated. You might want to use ergonomic accessories like padded wrist supports or document holders between your monitor and keyboard.
Regular ergonomic checks become crucial as workplace needs change. Organizations that monitor and adjust workstation setups consistently can reduce work-related injuries and promote a more comfortable and productive environment.
Chemical Handling Safety

Image Source: UF Environmental Health and Safety – University of Florida
Chemical safety is vital in workplaces. Poor handling practices caused over 420,000 workplace accidents with back injuries in 1999. Organizations can reduce chemical-related incidents by a lot through complete protocols and careful oversight.
Chemical Storage Fundamentals Chemical segregation is a vital part of safety. You should store acids in dedicated corrosive cabinets and keep organic and inorganic variants separate. Fire-rated cabinets are needed to store flammable materials. The quantity should not exceed 10 gallons outside storage areas. All containers need proper seals and hazard warning labels.
Essential Safety Protocols Chemicals can enter the body in several ways: through breathing, skin contact, swallowing, or injection. Here are the basic practices to lower risks:
- Keep detailed chemical inventories
- Use proper engineering controls like fume hoods
- Check equipment regularly
- Store chemicals below shoulder height
- Make emergency response equipment easy to reach
Emergency Response Guidelines Quick action is vital when chemical exposure happens. If chemicals get in your eyes, flush them with water for 15 minutes and take out contact lenses. For skin exposure, take off contaminated clothes right away and wash affected areas well. Keep spill control materials, neutralizing agents and absorbents close by.
Ventilation Requirements Good ventilation plays a key role in chemical safety. Labs must have at least seven air changes every hour. Local exhaust systems should be installed where dangerous vapors might collect, especially in areas with volatile substances. Regular checks and maintenance keep ventilation systems working at their best.
Training and Documentation OSHA requires complete training for anyone who handles dangerous chemicals. Workers must know about:
- How to spot chemical hazards
- The right handling steps
- What to do in emergencies
- How to use protective equipment
- Ways to contain spills
Regular safety meetings and following these rules help organizations build a safety-focused culture and meet regulations.
Machine Safety Protocols

Image Source: ISHN.com
Machine inspections are the foundations of workplace safety. OSHA data shows that poor equipment maintenance leads to many preventable accidents. Organizations can minimize risks by following proper protocols.
Equipment Inspection
Heavy construction equipment needs daily inspections. Key checks include:
- Control mechanisms for maladjustments
- Hydraulic systems for proper fluid levels
- Electrical components for signs of deterioration
- Tires for proper inflation during use
Qualified staff must document and keep monthly inspection records for at least three months. These checks confirm that equipment matches the manufacturer’s specifications and performs well during operation.
Safe Operation Guidelines
Machine operators need to follow strict protocols to avoid accidents. They should check if all wiring components in hazardous areas maintain dust-tight, dust-ignition-proof conditions. The staff must also secure floor-mounted machines properly to prevent movement.
Maintenance staff can operate equipment only in two situations:
- When they need to verify maintenance
- When qualified operators directly supervise them
Maintenance Requirements
Detailed maintenance strategies help equipment last longer. Teams should use condition-based monitoring with sensors that measure temperature, vibration, and operational variables. A routine maintenance schedule should include:
Daily Care: Equipment needs regular cleaning, lubrication, and visual inspections while in service. These tasks prevent failures without increasing costs.
Proactive Measures: Teams should make use of information to manage potential failures through Failure Mode Effect Analysis (FMEA). This method helps spot issues early and reduces unexpected downtime.
Documentation Requirements: Maintenance records must include:
- Items checked and inspection results
- Inspector’s name and signature
- Inspection date
- Required follow-up actions
Organizations can build a culture of machine safety and meet regulations by following these protocols and holding regular safety meetings.
Fall Protection Measures

Image Source: BigRentz
Falls are still the main cause of construction worker deaths. OSHA requires fall protection when working at heights of six feet in construction and four feet in general industry workplaces. Organizations can minimize these risks with the right safety measures.
Height Safety Equipment
Full body harnesses spread fall arrest forces across shoulders, thighs, and pelvis. Here’s what you need:
Anchorage Systems: These must support 5,000 pounds per attached employee. They serve as secure points that connect lifelines, lanyards, or deceleration devices.
Connecting Devices: Energy-absorbing lanyards, self-retracting devices, and rope adjusters connect harnesses to anchorage points. The arresting force on workers must never exceed 1,800 pounds.
Safe Climbing Practices
The three-point contact rule is crucial – keep two hands and one foot, or two feet and one hand, on the ladder. You’ll need special equipment to transport tools:
- Hoist buckets with proper load ratings
- Tool pouches attached to fall protection
- Holsters designed for elevated work
Engineers must design all containers to support intended gear weight with high-confidence safety factors of 5-to-1.
Rescue Procedures
Time is critical during fall incidents because suspension trauma can be fatal within 30 minutes. ANSI Standard Z359 requires rescue completion within six minutes of fall arrest. You must have this rescue equipment:
On-site Requirements:
- Rescue poles and ropes
- Lifting devices
- Aerial lifts
- Self-rescue equipment
Organizations must create rescue plans before work begins. These plans need details about:
- Emergency contact procedures
- Available equipment locations
- Qualified personnel responsibilities
- Medical evaluation protocols
Complete fall protection measures and regular safety meetings help create secure work environments. Note that prevention is key – proper training, equipment inspection, and hazard assessment reduce fall risks by a lot.
Vehicle and Equipment Safety
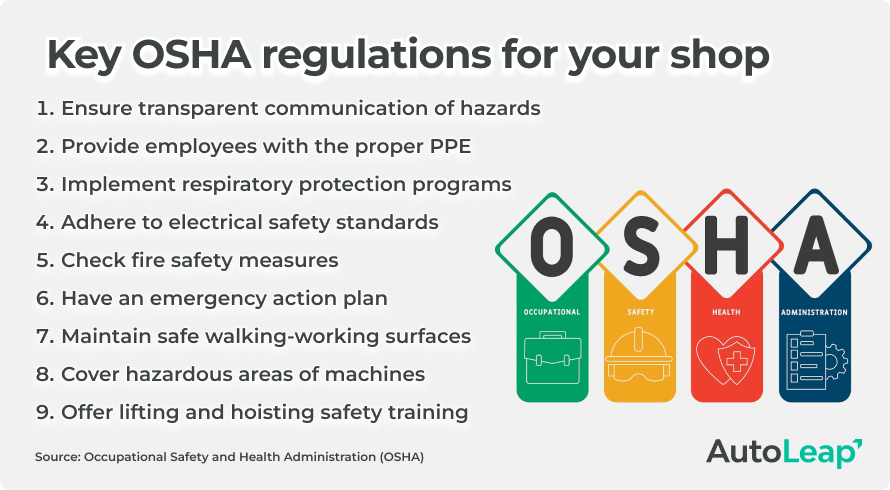
Image Source: AutoLeap
Vehicle inspections help prevent workplace accidents. OSHA requires detailed checks before each work day starts. Organizations can protect their workers and equipment by following systematic safety protocols.
Pre-operation Checks
Daily vehicle inspections must check several components. The fluid levels need regular monitoring – engine oil, brake fluid, radiator coolant, battery water, and fuel. Operators should check:
Critical Systems:
- Brake functionality, both service and parking
- Steering mechanism responsiveness
- Coupling devices integrity
- Safety devices operation
- Operating controls performance
Safe Operating Procedures
Safety protocols need strict compliance. Operators must have valid licenses that match their equipment type. Speed limits should stay under 10 mph on campus unless posted signs say otherwise. Backing operations need a dedicated observer to ensure safe reverse movement.
Everyone must wear seat belts – both operators and passengers. Equipment operators also need to:
- Keep operating manuals in vehicle cabs
- Maintain clean windshields free of cracks
- Follow manufacturer recommendations for passenger limits
- Use properly trained flag persons where necessary
Maintenance Schedules
Regular preventive maintenance keeps equipment running longer. Monthly inspections should check:
- Battery health and terminal connections
- Belt and hose conditions
- Chassis and joint lubrication needs
- Suspension system integrity
- Brake line conditions
Semi-annual maintenance needs more detailed evaluations including:
- Fluid system flushes
- Drive shaft inspections
- Diesel particulate filter cleaning
- Turbocharger performance checks
- Electrical system evaluations
Good maintenance records help organizations track their equipment’s health. This approach helps spot potential problems early and reduces unexpected breakdowns and costs.
Emergency Response Protocols
Image Source: OSHA
Quick action during emergencies saves lives, reduces property damage, and builds workplace resilience. FEMA’s data shows how training and education help people manage disasters better.
Emergency Types
A workplace emergency includes any unexpected situation that puts employees, customers, or operations at risk. Here are common scenarios you should know about:
Natural Disasters: Earthquakes, floods, hurricanes, and severe weather events just need wide-ranging readiness protocols. These unpredictable events affect logistics and need complete preparation.
Workplace Incidents: Chemical spills, gas leaks, and machinery breakdowns need quick response. Organizations can minimize damage with the right protocols.
Response Procedures
The Center for Domestic Preparedness gives more than 50 training courses that focus on incident management and mass casualty response. Key response elements should:
- Set up clear chains of command
- Name emergency coordinators
- Create evacuation routes
- Set up assembly points
- Keep emergency equipment ready
Emergency coordinators must quickly assess the situation and alert appropriate emergency responders when notified. They then take headcounts at rally points to make sure everyone got out safely.
Communication Channels
Research shows information becomes as vital as food or water during incidents. Good emergency communications need:
Multiple Communication Tools:
- Voice messages and immediate calling
- Text messaging services
- Two-way radios for nearby communication
- CB radios for area broadcasts
Message Components: Messages should tell you about specific hazards, locations, timing, warning sources, size of the threat, and safety guidelines. Social media and internet platforms help reach more people quickly.
The network works better when people keep non-emergency calls short and limited. Text messages often work better than voice calls in emergencies and help keep networks clear for critical communications.
First Aid Basics

Image Source: First Aid Product
Every seven seconds, an employee gets injured on the job. Organizations can minimize risks and stay compliant with regulations by having the right preparation and training in place.
Common Workplace Injuries
Workplace injuries show overexertion and bodily reactions leading with 1,001,440 cases, while contact with objects accounts for 780,690 incidents. Most strains happen because of wrong lifting techniques or equipment usage. On top of that, it’s the repetitive movements that cause most injuries in administrative and manufacturing work.
Treatment Protocols
First aid is the emergency care you give someone who’s injured or suddenly ill before medical help arrives. Here are the most important treatment guidelines:
Immediate Response Actions:
- Assess the victim’s condition
- Call emergency medical services
- Perform CPR if breathing stops
- Apply direct pressure to control bleeding
- Immobilize fractures
Medical professionals should check even minor incidents because complications can show up within 24 hours after injury. Good documentation is vital – you need to record incident details, treatments given, and what doctors recommend.
Emergency Contact Information
Your organization needs up-to-date emergency contacts for each employee. Here’s what you must have:
Required Information:
- Primary emergency contact name and relationship
- Secondary contact details
- Primary care physician information
- Health insurance provider details
- Known allergies and medications
HR teams should update this information yearly using data quality software to ensure accuracy. Companies without proper emergency response protocols face potential liability. A complete first aid program and regular safety meetings are the foundations of workplace security.
Good training and preparation help organizations respond quickly to workplace injuries. Note that OSHA requires reporting serious incidents – deaths within 8 hours and hospitalizations within 24 hours. Regular safety meetings and detailed emergency protocols then become vital to workplace security.
Lifting and Manual Handling

Image Source: Nutting Carts and Trailers
Back injuries make up 20% of workplace injuries. Workers get hurt most often during lifting tasks, accounting for 75% of these injuries. Organizations can reduce these risks by using proper techniques and equipment.
Proper Lifting Techniques
The NIOSH lifting equation sets a maximum load of 51 pounds. This number changes based on how often you lift, twisting of your back, vertical distance, load distance from your body, movement distance, and how easy it is to grip. Here’s everything you need to know about safe lifting:
Pre-lift Assessment:
- Check the load’s stability and weight
- Make sure your path is clear
- Stand with feet shoulder-width apart
- Stay close to what you’re lifting
Execution Steps: Keep the load near your waist as you lift. Put the heaviest part next to your body. Your back, hips, and knees should have a slight bend instead of a full flex or squat.
Weight Limits
OSHA hasn’t set exact weight limits, but NIOSH guidelines give different limits for men and women. Men should stay under 25 kg, while women’s limit is 16 kg. These rules work only when:
- You can grip the load easily
- Working conditions are good
- Your body stays stable
- You carry things less than 10 meters
Equipment Usage
The right equipment helps reduce injury risks by a lot. You might want to use:
- Hand trucks for heavy items
- Dollies for awkward loads
- Pushcarts to move things far
- Forklifts if you’re certified
Loads over 100 pounds need mechanical help. Pushing equipment works better than pulling it. Companies create safer workplaces and follow regulations by sticking to these rules and having regular safety meetings.
Confined Space Safety
Image Source: OSHA
Statistics show that confined spaces cause one fatality for every 10 accidents. Organizations can minimize these risks with detailed safety protocols.
Entry Procedures
Organizations must assess all spaces as permit-required confined spaces until pre-entry procedures prove otherwise. The essential pre-entry steps include:
Atmospheric Testing: The atmosphere must be tested in this sequence:
- Oxygen content (acceptable range: 19.5% – 23.5%)
- Combustible gasses (must be below 10% LFL)
- Toxic gasses (H2S below 10 ppm, CO under 25 ppm)
Documentation Requirements: The team must complete confined space entry permits that list hazard assessments, safety equipment needs, and communication protocols.
Monitoring Requirements
The atmosphere must be monitored continuously during confined space operations. Regular calibration of multi-gas detectors ensures accurate readings. Testing must cover these areas for spaces deeper than four feet:
- The worker’s surrounding area
- Four feet in the direction of travel
- Each side of the work area
Deep spaces or areas leading away from entry points might have layered atmospheres that need special attention.
Emergency Protocols
Rescue operations must be completed within six minutes of the incident according to ANSI standards. The key emergency response elements include:
Rescue Equipment:
- Rescue tripods with proper load ratings
- Full-body harnesses meeting safety standards
- Communication devices for constant contact
- Non-entry rescue equipment whenever feasible
Response Procedures: Workers must evacuate the space immediately if hazardous atmosphere is detected. The team must assess how the hazardous atmosphere developed and implement protective measures before allowing re-entry.
Organizations can maintain secure work environments through proper confined space protocols and regular safety meetings. Note that permit-required confined spaces just need written programs that detail entry procedures, hazard controls, and rescue protocols.
Hazard Communication

Image Source: Safety Emporium
The Hazard Communication Standard just needs clear information sharing about chemical hazards in workplaces. Organizations can stay compliant with regulations and promote secure work environments through proper implementation.
Warning Signs
OSHA recognizes several safety sign categories based on how severe the hazard is. Red, black, and white combinations show immediate dangers, while yellow and black point out potential hazards. The most important sign types include:
Danger Signs: Warn about major hazards that could lead to death Caution Signs: Alert workers about moderate risks Safety Instruction Signs: Provide general safety guidelines Biological Hazard Signs: Mark biohazard presence
Safety Data Sheets
Safety Data Sheets (SDS) share detailed hazard information in a standard 16-section format. The key sections have:
Identification: Lists chemical names, recommended uses Hazard Identification: Details warning information Composition: Specifies ingredients, stabilizing additives First Aid: Outlines original care protocols Fire Fighting: Provides response recommendations Accidental Release: Details spill management procedures
Communication Methods
You need multiple approaches to make hazard communication work. Employers must get SDSs for every hazardous substance they use or store. Organizations should also:
- Keep SDSs available in work areas
- Provide training in workers’ native languages
- Document chemical inventories completely
- Update safety protocols regularly
Training programs must cover hazard identification, proper handling procedures, and emergency response protocols to work well. Organizations help workers understand chemical risks better through consistent guideline adherence and regular safety meetings.
Note that employers risk liability without proper hazard communication systems. OSHA requires SDSs to be available to employees for all workplace hazardous chemicals. A complete communication protocol is the foundation of workplace security.
Tool Safety

Image Source: YouTube
Workplace injuries from hand and power tools exceed one million cases each year. These incidents cost organizations $15.40 million in medical expenses and lost productivity. Organizations can minimize these risks with complete safety protocols.
Hand Tool Safety
Most hand tool injuries happen because of misuse and poor maintenance. Here’s what you need to stay safe:
Selection Guidelines: Quality tools should match each specific task. Steel hand tools need heat treatment, and wrenches must have proper jaw alignment to avoid slippage. You should check tools before use. Look for mushroomed heads on impact tools, damaged wooden handles, and sprung wrench jaws.
Power Tool Guidelines
Power tools need extra safety measures. Start with proper grounding using three-wire cords or double insulation. Here are the key protocols:
Operation Requirements:
- Unplug tools before servicing or changing accessories
- Keep proper footing and balance
- Use clamps or vises to secure work
- Take damaged tools out of service right away
Guards must cover the entire blade on circular saws over 2 inches in diameter. Retractable lower guards should protect the teeth except at cutting points.
Maintenance Requirements
Regular maintenance keeps tools safe and extends their life. You need to keep inspection records for three months. Here’s what matters most:
Daily Procedures: Check if guards work properly and work rests stay 1/8-inch from wheels. Make sure disconnect switches lock in OFF positions. Clean your tools well and store them in dry places away from chemicals and high humidity.
Professional Service: Complex equipment needs regular professional maintenance. Qualified technicians should handle detailed inspections, calibrations, and preventive maintenance that’s beyond the core team’s abilities.
Organizations can promote secure work environments with proper tool safety protocols and regular safety meetings. Note that employers are responsible for tool condition, but employees must understand proper usage through complete training programs.
Weather-Related Safety

Image Source: Perry Weather
Weather conditions can directly affect workplace safety. The Bureau of Labor Statistics reports about 60 employees die each year from weather-related causes. Organizations protect their workforce against extreme conditions with detailed safety protocols.
Hot Weather Protocols
Heat-related illnesses can be deadly. Almost 75% of heat illness deaths happen during the first week on the job. Workers just need to follow the 20% Rule to stay safe. This means limiting first-day heat exposure to 20% of shift duration at full intensity and increasing it by no more than 20% each day.
Employers should take these steps to protect workers:
- Give cool drinking water and tell workers to drink one cup every 20 minutes
- Set up regular rest breaks in shaded spots
- Watch for heat illness signs like fainting, dizziness, and nausea
- Create emergency plans to handle heat-related issues
Cold Weather Guidelines
Cold stress happens due to low temperatures, wind chill, and wet conditions. Workers need three specific layers to stay protected:
- Inner layer: wool, silk, or synthetic material that keeps moisture away
- Middle layer: wool or synthetic that provides insulation
- Outer layer: protection from wind and rain that allows ventilation
Workers must know the signs of cold stress. These include reddening skin, tingling, pain, swelling, and leg cramps. Break areas should stay warm, and hot liquids should be available during shifts.
Storm Procedures
Lightning creates serious risks and strikes 300 people yearly in the United States. Workers must head to shelter right away when they hear thunder, even distant rumbles. Safe places include:
- Buildings that are fully enclosed with electrical wiring and plumbing
- Hard-topped metal vehicles with windows rolled up
Stay in shelter for at least 30 minutes after the last thunder. Stop crane operations and work at heights when winds get too strong. Make sure to secure temporary structures, framework, and equipment to prevent falling objects.
Organizations can maintain safe work environments in all weather conditions by using proper safety protocols and holding regular safety meetings. Note that OSHA requires employers to provide workplaces without any known weather-related hazards.
Workplace Violence Prevention

Image Source: Guardian Defense
Workplace violence is a serious threat. One in six violent crimes happen at work. Organizations can minimize these risks with complete prevention strategies.
Warning Signs
You need to spot warning signs early to prevent violent incidents. People often demonstrate physical indicators through:
Behavioral Changes: Watch for excessive absences, lower productivity and focus problems. Argumentative behavior can signal potential issues. Multiple warning signs require immediate action.
Physical Signs: Look for flushed faces, sweating, trembling and clenched fists. Violent gestures are red flags. Changes in voice patterns like loud talking or chanting can indicate trouble. People may also invade personal space.
Response Procedures
Quick intervention is vital when you spot threatening behavior. Organizations should implement:
Immediate Actions:
- Protect your personal safety first
- Call law enforcement right away
- Document all behaviors
- Tell supervisors immediately
Organizations should install video cameras, extra lighting and alarm systems for better protection. They also need ID badges, electronic keys and security guards.
Reporting Protocol
A solid reporting system helps document incidents properly. Here’s what you need:
Documentation Requirements: Keep detailed records of incidents, interventions and follow-up actions. Standard forms help organizations track trends and evaluate their prevention efforts.
Communication Channels: Make reporting methods available and allow anonymous submissions. Staff should feel safe to report without fear of retaliation.
Regular safety meetings and proper violence prevention protocols create secure workplaces. Note that OSHA requires employers to provide workplaces free from known hazards. A complete prevention program is the foundation of workplace security.
Mental Health Awareness
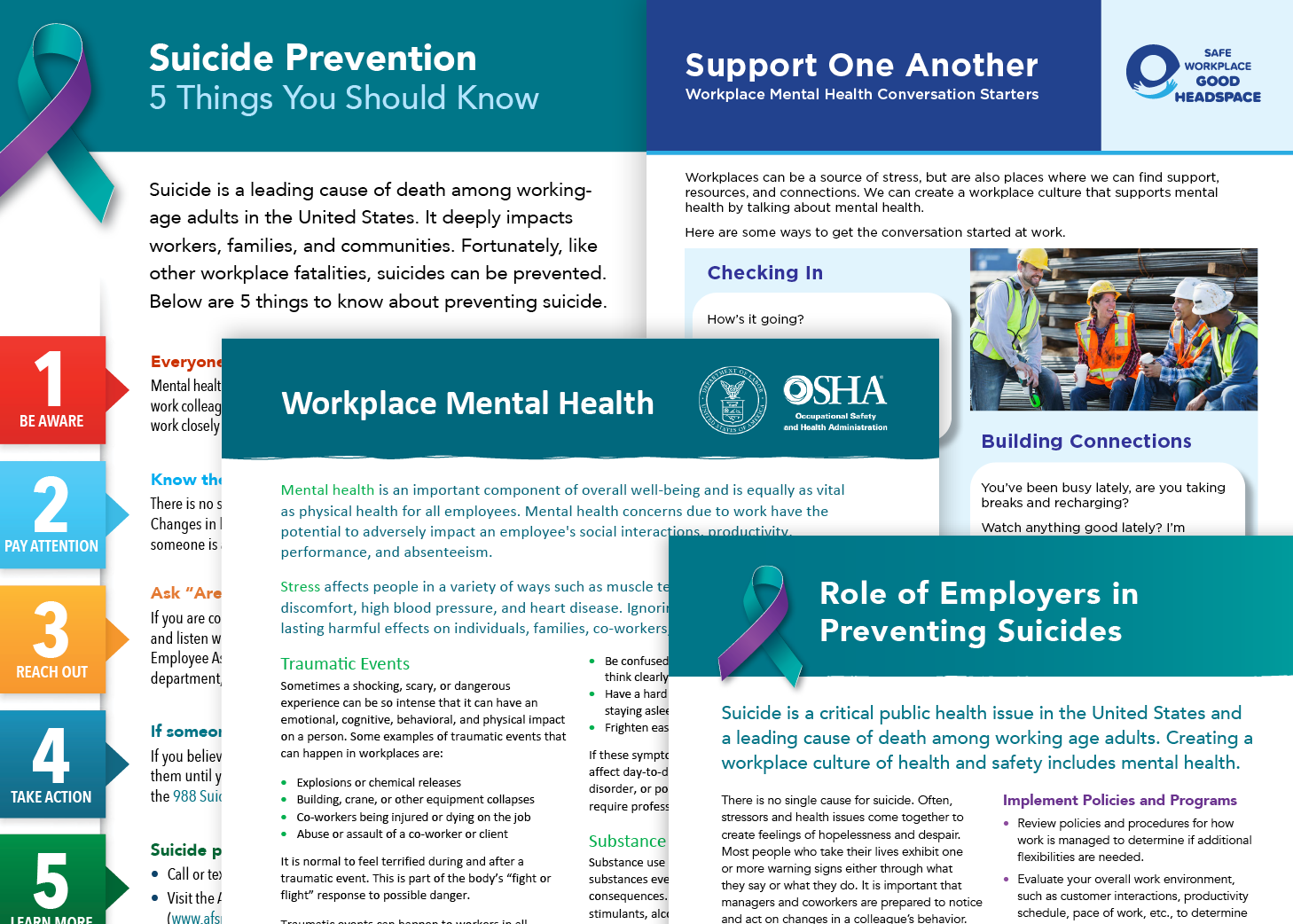
Image Source: OSHA
Mental health issues affect one in five U.S. workers, leading to four times more unplanned absences. Organizations encourage supportive environments and maintain productivity through detailed awareness programs.
Stress Management
Recent studies show workplace stress continues to be the most important source of employee distress. Management strategies must address four main workplace needs:
- Task demands with job security and workload
- Role demands covering conflicts and ambiguity
- Physical demands including workplace conditions
- Interpersonal demands including leadership styles
Organizations implement both proactive and reactive interventions to reduce stress effectively. Primary interventions prevent stress through wellness programs, while secondary interventions help remove risk factors through job redesign.
Support Resources
The National Behavioral Health Crisis Care Guidance provides detailed support through three core elements:
Someone to Contact: Services like the 988 Lifeline are immediately available. On top of that, mobile crisis teams deliver rapid, on-site interventions that connect people with appropriate care resources.
Safe Places for Help: Organizations must establish stabilization services that provide immediate treatment and prevention support. Employers should also implement detailed Employee Assistance Programs that offer:
- Online and telephone support options
- Help with stress and anxiety
- Support for caregiver needs
- Financial and legal guidance
Crisis Response
Crisis behavioral health services help people avoid psychiatric hospitalization and reduce emergency department interventions. Organizations must take these steps when identifying mental health emergencies:
Immediate Actions:
- Contact behavioral health professionals promptly
- Employ trained crisis responders
- Provide medication when necessary
- Arrange facility care if community support isn’t enough
Organizations maintain supportive environments through proper mental health awareness protocols and regular safety meetings. Note that studies show employees are three times more engaged when employers show concern for overall wellbeing.
Remote Work Safety

Image Source: Blue Lion HR Consulting
Remote workers deal with unique safety challenges. A well-planned workspace setup is vital to prevent injuries and boost productivity. Organizations can protect their remote teams with complete safety protocols.
Home Office Setup
Your workspace location plays a significant role. Pick a dedicated area with plenty of natural light to reduce eye strain and help you focus better. You’ll need these basic items:
Workspace Requirements:
- A sturdy desk with enough room for equipment
- Quality chair that supports your lower back
- External monitor at eye level
- Separate keyboard and mouse if you use a laptop
Environmental Considerations: Put your computer screens at right angles to windows to cut down on glare. Good airflow and proper task lighting will help you see better.
Ergonomic Guidelines
Your posture matters throughout the day. Line up the ‘B’ key on your keyboard with your belly button. Make sure you:
Optimal Positioning:
- Keep thighs parallel to floor
- Sit with your back straight against the chair
- Relax your shoulders with elbows at 90 degrees
- Plant feet flat on ground or use a footrest
Quick breaks every 30 minutes will help. Mix in some stretches and movement. The 20-20-20 rule works well – look 20 feet away for 20 seconds every 20 minutes to rest your eyes.
Emergency Procedures
Remote workers should be ready for different types of emergencies. Here’s what you need:
Emergency Planning: Make detailed evacuation plans and practice your fire escape routes often. Keep these emergency supplies handy:
- First aid materials
- Backup power sources
- Communication devices
- Emergency contact information
Documentation Requirements: List all business assets you need to protect during disasters. Save important work data in secure cloud systems and keep mobile hotspots ready for backup internet. Regular virtual safety meetings and proper remote work protocols help organizations protect their teams, no matter where they work.
Waste Management
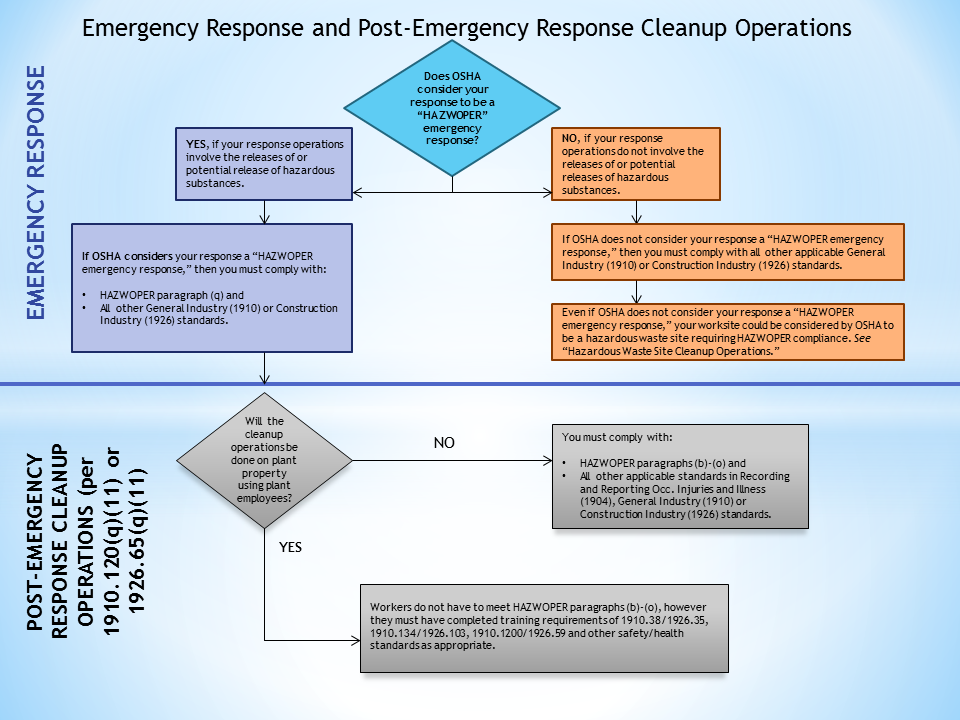
Image Source: OSHA
Good waste management protocols protect workers and the environment. Studies show that liquid and solid products often leak into surroundings during transfers. Organizations can lower these risks with systematic approaches.
Spill Prevention
Construction sites must have stormwater discharge permits and chemical spill prevention procedures by federal law. The most significant prevention measures have:
Storage Guidelines: Materials need storage in covered areas with secondary containment structures. Clear labels and Safety Data Sheets should be easily accessible. Leak detection devices, overflow controls, and diversion berms give better protection.
Air Quality
The world mishandles almost 50% of its waste. This leads to open dumping and burning that releases harmful substances. Good waste management just needs:
- Regular recycling
- Organic material composting
- Safe treatment methods
- Right disposal practices
Live Work Procedures
Workers must stick to strict protocols when they handle hazardous materials. If they find spills, they should use spill kits right away. These kits have absorbent pads, sorbent booms, and protective clothing.
PPE Requirements
Every employee who handles waste materials must wear proper protective gear. The basic equipment has:
- Heavy-duty gloves to prevent bloodborne pathogen exposure
- Cut-resistant boots with slip-resistant soles
- Face masks based on the job
- Industrial aprons to block contamination
Emergency Response
Quick action is vital during spill incidents. Every organization’s spill kits should be clearly labeled with these basics:
- Absorbent granular material
- Protective clothing with latex gloves
- Thick plastic garbage bags
- Drain covers
The quickest way to respond is to keep detailed records of where incidents happen, when they occur, and what materials spill. Regular training sessions should cover spill prevention and control measures. On top of that, periodic refresher courses help keep the workforce ready.
Comparison Table
Safety Topic | Key Risks | Essential Requirements | Training/Documentation | Emergency Response |
---|---|---|---|---|
Physical Safety Fundamentals | Workplace noise (61-100 dB), extreme temperatures, electrical hazards | Control hierarchy, engineering solutions, safe work practices | New hire instruction, yearly retraining for specific hazards | Spot and fix hazards before injuries happen |
Electrical Safety Protocol | Shock incidents (30,000/year), burns, electrocution | Good grounding, minimum 10ft distance from power lines, qualified personnel checks | Training limited to qualified personnel | Quick power shutoff, use non-conductive objects for rescue |
Fire Safety and Prevention | Office/store fires ($932M damage in 2020) | Regular risk checks, clear evacuation routes, assigned wardens | First-time and yearly fire extinguisher training | Quick evacuation, 150ft minimum distance from building |
PPE | Over 1,000 injuries yearly from poor PPE | Equipment meeting ANSI/ASTM standards, proper storage rules | Native language training, proof of understanding | Take off contaminated PPE right away, replace damaged items |
Ergonomic Safety | 30% of worker injury cases are MSDs | Right monitor placement, keyboard setup, regular breaks | Not specifically mentioned | 3-5 minute breaks every 30 minutes |
Chemical Handling | 420,000 workplace accidents yearly | Right segregation, ventilation (7 air changes/hour), item lists | OSHA-required training | 15-minute water flush for eye contact, remove clothes right away |
Machine Safety | Not specifically quantified | Daily checks, proper anchoring, dust-tight conditions | Monthly recorded inspections | Quick equipment shutdown for problems |
Fall Protection | Leading cause of construction deaths | 5,000 lb anchorage support, full body harnesses | Rescue planning before work | 6-minute rescue completion needed |
Vehicle/Equipment Safety | Not specifically quantified | Pre-operation checks, speed under 10mph, valid licenses | Regular maintenance records | Dedicated spotter for backing up |
Emergency Response | Multiple scenarios including natural disasters | Clear command chain, assigned coordinators, escape routes | 50+ training courses ready | Quick situation check, headcount at meeting points |
First Aid | One injury every seven seconds | Updated emergency contacts, treatment steps | Yearly information updates | Check even small incidents within 24 hours |
Lifting/Manual Handling | 1 in 5 workplace injuries | Maximum 51 lbs load (NIOSH), right technique | Not specifically mentioned | Use mechanical help for loads over 100 lbs |
Confined Space Safety | 1 in 10 accidents lead to death | Air testing, ongoing monitoring | Written programs needed | 6-minute rescue completion needed |
Hazard Communication | Not specifically quantified | Easy access to SDS, clear signs, chemical lists | Native language training needed | Detailed emergency steps in SDS |
Tool Safety | Over 1M injuries yearly ($15.4M cost) | Regular checks, proper grounding, working guards | Detailed training programs | Remove damaged tools right away |
Weather Safety | 60 deaths yearly | 20% Rule for heat exposure, three-layer clothing system | Not specifically mentioned | 30-minute wait after last thunder |
Workplace Violence | 1 in 6 violent crimes happen at work | Video monitoring, ID badges, security systems | Standard report forms | Call law enforcement right away |
Mental Health | Affects 1 in 5 workers | EAP programs, support resources, wellness programs | Not specifically mentioned | Call behavioral health experts |
Remote Work | Not specifically quantified | Personal workspace, proper ergonomic setup | Not specifically mentioned | Clear evacuation plans, emergency supplies |
Waste Management | Not specifically quantified | Backup containment, clear labels, spill prevention | Regular training sessions | Quick spill control steps |