American workplaces lose 15 workers each day who never return home to their families. Worker fatalities have dropped by a lot since 1970, when 38 people died daily. Yet workplace safety violations remain a serious risk in industries of all types.
OSHA’s 2023 violation statistics paint a concerning picture. Fall protection tops the list with 7,271 violations. Companies face fines up to $145,027 for each violation. Workplace safety compliance protects both lives and your business’s future. OSHA’s budget increase to $632 million in 2023 points to tougher enforcement coming soon.
Our analysis covers the costliest and most frequent OSHA violations you should watch for in 2025. Hazard communication failures can cost over $98,000, while poor training documentation might set you back $55,000 or more. This piece explains these violation costs and shows you how to stay compliant effectively.
Fall Protection Violations: The $145,027 Mistake

Image Source: SafeRack
Fall protection violations remain OSHA’s most cited workplace safety standard. This marks the 13th straight year at the top with 7,271 violations in 2023. The numbers grow even higher with 2,112 violations linked to fall protection training requirements, pushing the total to nearly 9,400 citations.
Typical Fall Protection Violation Scenarios
OSHA requires fall protection for construction workers who work 6 feet or higher above lower levels. Workers often lack proper protection near unprotected floor holes. Missing guardrails around elevated surfaces and insufficient safety equipment for suspended workers are common problems. Many employers fail to protect workers near dangerous equipment, even when heights are below 6 feet.
Cost Breakdown: Fines, Legal Fees, and Workers’ Compensation
Violation costs go well beyond the original fines. A single fracture from a fall costs about $54,856 in direct expenses and $60,341 in indirect costs, adding up to $115,197. Companies that show willful or repeated violations face penalties up to $165,514 per case. One construction company paid a record $1.2 million fine for 13 fall protection violations after a worker’s fatal fall.
Industry Impact Statistics
Falls continue to be the leading cause of deaths in construction, making up about one-third of all industry fatalities. Slip, trip, and fall incidents caused 18% of all non-fatal work injuries in 2021, with workers missing an average of 14 workdays. These fall-related injuries led to 16% of all work-related deaths that year.
Prevention and Compliance Strategies
Companies must put in place complete fall protection systems that include guardrails, safety nets, or personal fall arrest systems. Key steps to comply include:
- Check fall protection equipment before each use
- Train workers on equipment use and its limits
- Create written fall protection plans that spell out hazards and safety measures
- Set up proper guardrails and toe-boards around elevated surfaces
Hazard Communication Failures: $98,000+ Per Instance

Image Source: eLeaP
HazCom violations jumped 19% in 2023, reaching 3,213 documented cases across workplaces. Businesses failed to properly tell their employees about chemical hazards, leading to these violations.
Common HazCom Violation Types
Incomplete written programs topped the list with 783 documented cases. Poor employee education about chemical hazards led to 708 training violations. Companies couldn’t provide easy access to Safety Data Sheets (SDS), resulting in 285 violations. Missing SDSs for specific chemicals added another 198 cases. Poor chemical inventory management created 182 more violations.
Direct and Indirect Cost Analysis
OSHA raised its maximum penalties for serious violations to $15,625 per instance. This meant HazCom violations in 2023 could exceed $50.2 million in total penalties. Hidden costs include workers’ compensation claims, reduced productivity, damaged equipment, and legal expenses. Staff time adds another hidden cost – employees spend about 3 hours each week handling SDS documentation.
Compliance Requirements
Employers must follow these key elements to stay compliant:
- Create and update a written hazard communication program that lists all workplace hazardous chemicals
- Label chemical containers with clear hazard warnings
- Keep current Safety Data Sheets ready for all employees to access
- Give detailed employee training about chemical hazards and protection measures
Chemical manufacturers must assess and classify their products’ hazards. Employers need to share this information with workers through labels, safety data sheets, and training programs. The training should cover how to spot hazards, use proper protection, and handle emergencies.
OSHA makes it clear that searching online for SDS during emergencies doesn’t work. Companies must keep specific SDS libraries for their workplace chemicals where workers can find them quickly. Smart organizations update their chemical lists often and check that safety documents stay current.
Machine Guarding Negligence: $85,000 Average Penalty

Image Source: RPF Environmental
Safety violations related to machine guarding continue to pose serious risks, with companies facing penalties of $85,000 for each case. A real-life incident at North American Lighting saw a master maintenance technician suffer severe facial burns after pressurized material exploded in a plastic molding machine.
Violation Categories and Associated Costs
OSHA’s machine guarding standards require protection against hazards from point of operation, ingoing nip points, rotating parts, flying chips, and sparks. Companies now face penalties of $16,550 for serious violations that could lead to death or substantial physical harm. The stakes rise even higher for willful or repeated violations, with fines reaching $165,514 per case.
Equipment-Specific Requirements
OSHA regulations specify distinct guarding requirements for different machines:
- Power presses and milling machines
- Woodworking equipment and power saws
- Forming rolls and calenders
- Portable power tools
Companies must permanently attach guards to machines whenever possible. If permanent attachment isn’t practical, they need to secure the guards elsewhere. Employers must use fixed guards, interlocked guards, adjustable guards, or self-adjusting guards to protect against point-of-operation hazards.
Affordable Compliance Solutions
Machine guarding violations create significant indirect costs beyond OSHA penalties:
- Workers’ compensation claims from amputations and injuries
- Lost productivity and equipment damage expenses
- Legal fees and compliance costs
- Lower employee morale
Organizations should assess their equipment risks regularly to maintain compliance. Key preventive steps include:
- Installing proper guards on all hazardous machine parts
- Giving detailed operator training on safeguarding procedures
- Creating detailed energy control protocols
- Conducting routine equipment inspections
U.S. workplaces received 985 citations and $6.9 million in penalties for machine guarding violations. Proper guarding solutions prove more economical than dealing with violations, injuries, and their associated costs.
Respiratory Protection Oversights: $75,000+ in Fines
OSHA’s most cited standards show respiratory protection violations taking second place, with 2,527 citations in Northern Illinois alone. This rise shows how workplace respiratory hazards have become a major concern with serious financial consequences.
Violation Types and Financial Impact
OSHA’s new instance-by-instance citation policy, launched in March 2023, lets them issue separate penalties for each respiratory protection violation. Metal fabrication companies paid the highest price at $274,797 for 435 citations. The specialty trade contractors weren’t far behind, paying $261,689 for 398 violations.
The biggest problems include missing written medical evaluations, wrong respirator fit testing, and incomplete protection programs. A nursing facility had to pay $83,675 because they didn’t check respirator seals or conduct fit testing properly. One manufacturer faced even steeper fines of $587,564 for not giving workers proper respirators and skipping fit tests.
Implementation Costs vs. Violation Penalties
Non-compliance costs have reached new heights. Each serious violation now brings a $16,550 penalty. Companies that show willful or repeated violations might pay more than $156,000 each time. A shipbuilding company learned this lesson when they paid $370,358 for missing fit tests and medical evaluations.
Program Development Guidelines
Your respiratory protection program needs these key components:
- Medical evaluations before anyone uses a respirator
- Yearly fit testing for tight-fitting respirators
- Complete employee training on proper use
- Regular checks to see if the program works
- Clear steps to clean, store, and maintain respirators
Program administrators need proper training and experience to run things effectively. Companies must give their workers respirators, training, and medical evaluations free of charge. Regular workplace monitoring helps keep the program running smoothly and workers safe.
Lockout/Tagout Violations: $74,000 Per Citation

Image Source: Lockout Tagout
LOTO (Lockout/tagout) violations continue to be a big problem, with authorities issuing 2,554 citations in 2023 – a 17% increase from last year. A furniture manufacturer in Texas had to pay heavy penalties after an employee got injured due to gaps in their LOTO procedures.
Common LOTO Mistakes
Many companies take LOTO requirements too lightly and treat them as items to check off rather than vital safety protocols. These violations typically include:
- Missing energy control procedures for specific equipment
- Not enough lockout devices and hardware
- Using regular padlocks instead of industrial-grade safety locks
- Missing multiple energy sources that go beyond electrical isolation
True Cost of Non-Compliance
LOTO violations cost much more than just OSHA penalties. The death of a 33-year-old Spanish-speaking janitor inside a linen dryer shows these devastating outcomes. The financial damage includes:
- Higher insurance premiums and workers’ compensation claims
- Legal costs and business disruptions
- Damaged equipment and lost productivity
- Problems keeping employees
LOTO violations led to USD 1,052,245 in penalties from 149 inspections in 2017, with each citation averaging USD 4,698. A meat processing facility had to pay USD 278,000 after an employee fell into a corrosive chemical vat and suffered severe injuries.
Training Requirements and Solutions
OSHA requires detailed training for three different types of employees. Authorized employees need to know:
- How to spot hazardous energy sources
- Types and amounts of energy present
- Ways to isolate and control energy
Affected employees must learn about:
- Why energy control procedures matter
- How to recognize LOTO in use
- Why they shouldn’t touch LOTO devices
Companies must document all training with employee names and dates. Employees need retraining after job changes, equipment updates, or if regular checks show problems with procedures. Of course, proper LOTO procedures save about 120 lives and prevent 50,000 injuries every year.
Powered Industrial Truck Infractions: $70,000 Average Fine

Image Source: KPA
Businesses face average costs of $70,000 per citation for powered industrial truck violations. This reality became evident when Mohawk Industries had to pay $105,000 in penalties after a workplace death.
Violation Categories
The powered industrial truck standard ranks seventh in OSHA’s most violated safety regulations. Common violations include:
- Trucks operated with blocked forward views
- Untrained staff operating equipment
- Unsafe vehicles not removed from service
- Skipped pre-shift inspections
A facility reported serious violations when operators drove with raised loads. This led to several injuries and heavy fines. Companies must make sure their operators keep proper load heights and stick to safety protocols.
Cost Impact Analysis
Violation costs go far beyond the original fines. Each truck accident typically costs $118,211. These expenses cover:
- Medical costs and workers’ compensation
- Equipment repairs and replacements
- Legal expenses and higher insurance rates
- Lost productivity from delays
One company paid $70,000 in willful violation fines because operators drove with blocked views. They faced five more serious citations. Poor training and lockout/tagout procedures added another $35,000 in penalties.
Compliance Best Practices
OSHA requires complete operator training programs that must have:
- Formal classroom lectures and interactive sessions
- Hands-on practical training
- Regular performance checks
- Training completion certificates
Companies need to check operator skills through workplace evaluations every three years. Both staffing agencies and host employers must ensure proper training for temporary workers. Keeping detailed training records and doing regular equipment checks costs less than dealing with violations and their expenses.
Electrical Safety Violations: $68,000+ Per Instance
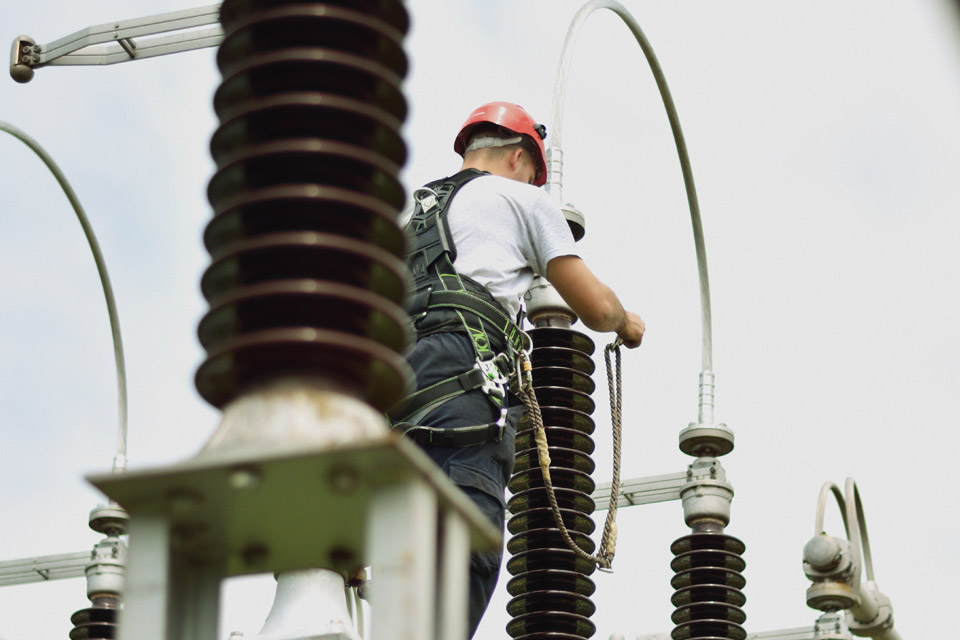
Image Source: Veriforce
Each year, electrical safety failures cause around 2,000 non-fatal injuries and claim 150 lives. A recent case highlights what this means – Sen-Dure Products, a cooling equipment manufacturer, received $68,000 in penalties for 24 safety violations.
Types of Electrical Violations
OSHA’s electrical standards focus on two main hazard categories. Physical contact with electrical conductors creates shock hazards. Short circuits release substantial electrical energy that leads to flash hazards. The most common violations include:
- Insufficient grounding path protection (502 violations)
- Inadequate ground fault protection (306 violations)
- Defective strain relief in flexible cords (232 violations)
- Worn or frayed electrical cables (216 violations)
Industry-Specific Costs
Manufacturing, retail, wholesale, lodging, food service, transportation, and warehousing sectors see frequent citations. Smith’s Electrical Service & Repair’s case shows the human cost – a 22-year-old worker suffered arc flash burns, resulting in $93,566 in penalties. The financial impact goes beyond immediate fines:
- Medical costs range from $200,000 to $1 million
- Litigation expenses typically run between $10-15 million
- Business losses average $800,000 per minute of downtime
- Additional costs come from equipment repair or replacement
Prevention Strategies
Safety compliance needs to cover both equipment and procedures:
- Install ground fault circuit interrupters where moisture exists
- Use proper insulation that meets voltage requirements
- Label all electrical panels and circuits clearly
- Follow strict lockout/tagout protocols
Qualified electricians must handle all wiring installations to meet safety standards. Companies should conduct regular inspections to spot potential hazards like damaged insulation or exposed electrical parts. Research from Aberdeen shows the stakes – 82% of companies that faced unplanned electrical downtime lost about $2 million in revenue.
Scaffolding Safety Failures: $65,000 Average Penalty

Image Source: Granite Industries
Construction workplace deaths from scaffold accidents remain alarmingly high. Data shows 46 workers lost their lives after falling from scaffolds in 2018 alone. The tragic ordeal at Fru-Con Construction Corporation demonstrates these dangers – a carpenter fell 82 feet to his death when a scaffold frame slid off its bracket.
Common Violation Scenarios
OSHA investigations show several patterns of scaffolding violations. The biggest problem comes from inadequate fall protection, especially on projects that exceed 10 feet in height. Everything in safety gets overlooked, including:
- Damaged or undersized planks on platforms
- Wrong scaffold assembly and modifications
- Loads that exceed maximum capacity
- Missing guardrail systems and toeboards
Financial Implications
OSHA penalties are nowhere near the complete financial impact of scaffold accidents. A scaffolding contractor faced USD 300,370 in fines after a worker’s fatal fall from a seven-story building. This is a big deal as it means that OSHA’s maximum penalties for serious violations rose to USD 16,550 per instance in 2025, with willful violations reaching USD 165,514.
Compliance Requirements
OSHA requires complete safety protocols for scaffold usage. A qualified person needs to inspect scaffolds before each work shift and after anything affects structural integrity. The core team must focus on:
- Platform Construction:
- Full planking between front uprights and guardrail supports
- Minimum 18-inch platform width
- Maximum one-inch space between platform and uprights
Workers need proper training to recognize hazards and follow safety procedures. Bad weather conditions like storms or high winds mean no scaffold work unless a competent person deems it safe and workers use personal fall arrest systems. Detailed inspection records and systematic safety protocols ended up being cheaper than dealing with violations and their costs.
Ladder Safety Negligence: $63,000+ in Fines

Image Source: KPA
Ladder accidents take 300 lives every year, and construction workers are at the highest risk. A company called Reconstruction Experts had to pay $63,000 as a willful violation penalty because they failed to protect their workers from cave-in hazards in trenches.
Violation Categories
OSHA has identified several dangerous ladder safety violations. The biggest problems come from workers using broken ladders, putting too much weight on them, and setting them up incorrectly. Many employers miss these basic requirements:
- Ladders need secure attachments at the top so they don’t slide
- Climbers must keep three points of contact
- The ladder setup must follow a 4:1 angle ratio
Cost Analysis
OSHA penalties are just the start of the financial burden. Starting January 2025, companies will pay up to $16,550 for each serious violation. This is a big deal as it means that willful or repeated violations can cost up to $165,514 per citation. One construction company learned this the hard way and paid $10,800 because they didn’t provide proper fall protection or extend their ladders correctly.
Hidden costs also include:
- Fall injury claims through workers’ compensation
- Work disruptions that reduce productivity
- Money spent replacing equipment
- Legal and compliance costs
Safety Program Implementation
OSHA requires detailed ladder inspection protocols. Companies must keep their ladders free of oil, grease, and anything that could cause slipping. A good program needs these key elements:
Competent staff members should check each ladder before work starts. Any ladder with structural problems needs a “Do Not Use” tag and immediate removal. Companies must keep detailed records of all inspections and fixes.
Fixed ladders need side rails that extend 3 feet above where workers step off. Ladders that don’t support themselves need placement on flat, stable ground. Workers must receive thorough training about choosing the right ladder, checking it properly, and climbing safely.
Eye and Face Protection Oversights: $60,000 Per Citation
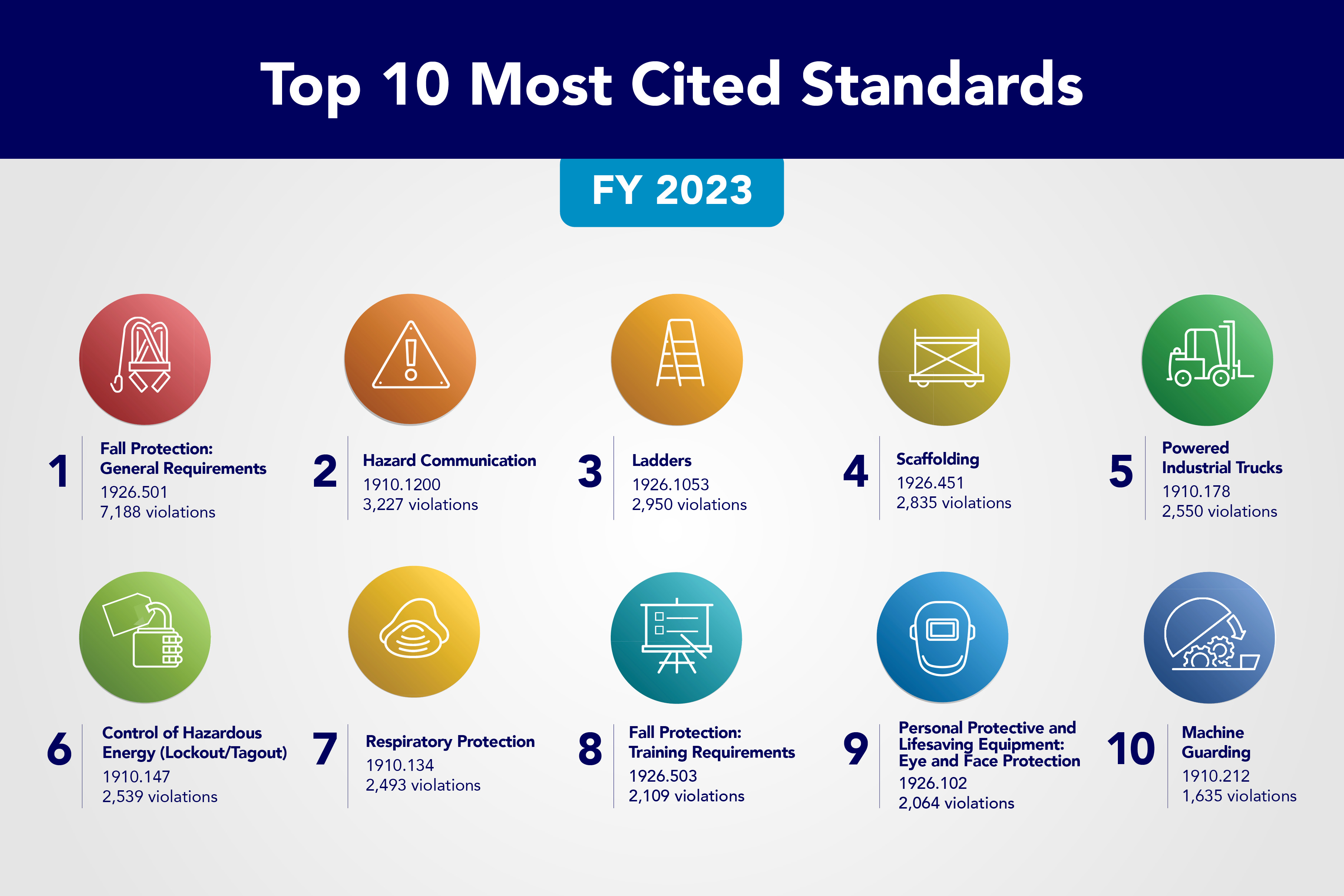
Image Source: OSHA
U.S. workers face thousands of preventable eye injuries each year. Medical treatment becomes necessary for about 2,000 workers daily due to workplace eye injuries. OSHA’s 2023 records show 1,698 eye and face protection citations from 1,691 inspections.
Violation Types
Specialty trade contractors paid the highest price with $4,099,758 in fines. Construction companies came next with $216,923 in penalties. The biggest problems come from:
- No proper assessment of eye and face risks
- Wrong choice of protective equipment
- Poor training on equipment use
- Skipping fit tests and equipment maintenance
Emergency departments treat one-third of all eye injuries. More than 100 cases lead to workers missing workdays. Tiny objects, smaller than a pinhead, cause most injuries by creating serious punctures, abrasions, and contusions.
Total Cost Impact
Eye injuries cost businesses over $300 million yearly in lost time, medical bills, and worker compensation. Companies face these expenses beyond OSHA penalties:
- Worker compensation payments up to $96,700 for losing an eye
- Medical costs between $22,800 and $301,870 based on state laws
- Production losses from worker disability
- Legal fees and higher insurance rates
Compliance Solutions
OSHA requires specific protection based on workplace risks:
- Safety spectacles with side shields protect against impacts
- Well-fitted goggles plus face shields guard against chemicals
- Special-purpose lenses with side protection shield from heat
Workers who need prescription lenses must have them built into their protective equipment. Every piece of eye and face PPE needs clear manufacturer identification marks. Companies stay compliant and avoid expensive violations by inspecting equipment regularly, maintaining it properly, and giving workers detailed training.
Emergency Response Plan Violations: $58,000 Average Fine
OSHA handed out 47 citations with penalties exceeding $115,000 last fiscal year because companies failed to create or maintain Emergency Action Plans. The stakes are even higher for healthcare organizations, where average fines have nearly doubled to $4,900 per citation.
Common Violations
A hydrochloric acid spill at Crescent Manufacturing revealed serious safety gaps during a recent inspection. These violations cover:
- Incomplete emergency response plans
- Untrained emergency responders
- No medical consultations for exposed employees
- Limited disaster resources
Cost Breakdown
OSHA penalties are just the beginning when it comes to emergency response plan violations. A manufacturing company faced $272,900 in proposed fines for 39 alleged violations. Companies should consider these financial risks:
- Willful violations can lead to direct penalties up to $124,709
- Each willful violation carries minimum fines of $8,908
- Companies with multiple locations face multiplied costs
Implementation Guidelines
Companies must follow specific OSHA requirements for emergency action plans. Written plans that detail emergency reporting and evacuation protocols are mandatory. Any organization with more than 10 employees needs written documentation.
These plans must include:
- Procedures for emergency evacuation and exit route assignments
- Protocols for employees operating critical equipment
- Methods to account for all personnel after evacuation
- Procedures for rescue and medical duties
- Contact information for emergency response coordinators
Employees need to review these plans at the time of development, when their responsibilities shift, and after any modifications. Organizations should also evaluate potential emergency scenarios and put site-specific safety measures in place. Regular audits play a vital role in finding gaps, regulatory issues, and work to be done that ensures compliance.
Training Documentation Failures: $55,000+ Per Instance

Image Source: The HIPAA Journal
Proper documentation is the life-blood of workplace safety compliance. Many organizations find it hard to maintain accurate training records. A recent OSHA investigation showed that employers often ignore the documentation they just need, which leads to big penalties.
Documentation Requirements
OSHA requires complete record-keeping for all safety training programs. Employers should keep detailed documents with each employee’s name, training dates, and trainer identification. Workers in permit-required confined spaces must have documents that prove their skills to work safely. Training records also must have written certification that shows employees understand safety protocols.
Violation Costs
Poor documentation costs nowhere near what you see in original penalties. Serious violations in 2025 will cost up to $16,550 each time. A manufacturing facility got hit with $272,900 in proposed penalties because they didn’t document employee safety training. Companies also face:
- Workers’ compensation claims that average $41,757 per whole ordeal
- Lost productivity costs $0.61 for every dollar spent on healthcare benefits
- Higher insurance premiums due to bad safety records
Record-Keeping Solutions
The quickest way to handle documentation needs an organized approach. Here are the foundations of good record-keeping:
Clear procedures help you retain control of documents. Training records must be kept throughout employment plus many more years. Digital tools simplify record management and make it easy to find documents during inspections.
Companies must track everything in safety training development:
- Who needs training and what they should learn
- Materials used and who developed them
- Training content and how it’s evaluated
Research shows employers save $4.00 to $6.00 for every dollar they put into good workplace safety documentation. Good records not only keep you compliant but also give you vital proof during liability claims or worker compensation disputes.
Comparison Table
Violation Type | Maximum/Average Fine | Citations (2023) | Primary Violation Types | Key Compliance Requirements |
---|---|---|---|---|
Fall Protection | $145,027 | 7,271 | Poor protection near floor openings, missing guardrails, lack of safety gear | Guardrails, safety nets, personal fall arrest systems above 6 feet |
Hazard Communication | $98,000+ | 3,213 | Missing written programs, gaps in training, limited SDS access | Written program, clear labeling, SDS updates, staff training |
Machine Guarding | $85,000 | 985 | Exposed operation points, dangerous nip points, unprotected rotating parts | Fixed guards, interlocked guards, adjustable guards, regular checks |
Respiratory Protection | $75,000+ | 2,527 | Poor medical checks, wrong fit testing, incomplete safety plans | Medical evaluations, yearly fit testing, staff training, program reviews |
Lockout/Tagout | $74,000 | 2,554 | Poor energy control steps, missing devices, wrong lock usage | Energy control steps, right hardware, staff training, certification |
Powered Industrial Trucks | $70,000 | Not mentioned | Blocked views, untrained staff, unsafe vehicles, missed checks | Staff training, hands-on demos, regular testing, certification |
Electrical Safety | $68,000+ | Not mentioned | Poor grounding, weak fault protection, broken strain relief | Good grounding, GFCI setup, clear labels, qualified experts |
Scaffolding Safety | $65,000 | Not mentioned | Missing fall protection, broken planks, wrong setup | Expert checks, full planking, 18-inch wide platforms |
Ladder Safety | $63,000+ | Not mentioned | Broken ladders, wrong placement, weight limit issues | Secure setup, 4:1 angle ratio, regular checks, proper training |
Eye/Face Protection | $60,000 | 1,698 | Missing hazard checks, wrong gear choices, poor training | Hazard-matched protection, fit testing, regular upkeep |
Emergency Response | $58,000 | 47 | Incomplete plans, untrained teams, no medical advice | Written plans, exit procedures, staff training, regular reviews |
Training Documentation | $55,000+ | Not mentioned | Missing records, incomplete logs, poor verification | Written proof, detailed records, trainer info, digital tools |
Conclusion
OSHA violations can destroy a company financially. Each violation costs between $55,000 to $145,027. Fall protection tops the violation list with 7,271 citations. Hazard communication failures and respiratory protection oversights come next.
The costs go way beyond the original fines. Companies face mounting medical bills, legal expenses, and workers’ compensation claims. Lost productivity adds to these expenses substantially. A worker’s injury can rack up total costs over $115,000. Fatal accidents push these costs into the millions.
Smart prevention costs nowhere near as much as penalties. Companies save $4-6 on every dollar they put into detailed safety programs, proper documentation, and regular training. Organizations with solid safety measures see 48% fewer workplace incidents. Their injury-related costs drop by half.
OSHA’s bigger 2025 budget points to tougher enforcement. Businesses just need to stay compliant through:
- Regular safety checks and risk assessments
- Detailed worker training programs
- Clear documentation systems
- Current emergency response plans
Workplace safety needs constant alertness. Every prevented accident saves workers’ lives and keeps businesses running. Smart companies see safety compliance as an investment that pays off, not just another expense.
FAQs
Fall protection violations were the most cited, with 7,271 citations issued in 2025. This includes inadequate protection near floor holes, missing guardrails, and insufficient safety equipment for workers at heights above 6 feet.
OSHA fines can be extremely costly, ranging from $55,000 to $145,027 per violation instance. For example, fall protection violations can result in fines up to $145,027, while hazard communication failures may cost over $98,000 per citation.
An effective workplace safety program should include regular safety audits, comprehensive employee training, detailed documentation systems, and up-to-date emergency response plans. Implementing these measures can significantly reduce workplace incidents and associated costs.
The frequency of safety training depends on the specific OSHA standard and workplace hazards. However, generally, employers should provide initial training for new employees, annual refresher courses, and additional training when job duties change or new equipment is introduced.
Beyond OSHA fines, neglecting workplace safety can lead to substantial indirect costs, including workers’ compensation claims, increased insurance premiums, legal expenses, equipment damage, lost productivity, and potential business closure. A single workplace injury can result in total expenses exceeding $115,000.